Calibração de manômetros: como garantir precisão nas medições
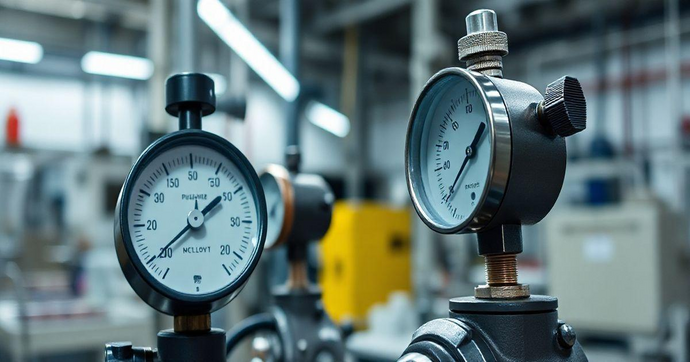
Por: Thiago - 15 de Janeiro de 2025
A calibração de manômetros é um processo fundamental para garantir a precisão e a confiabilidade das medições em diversos setores, como industrial, laboratorial e de saúde. Com o uso adequado desses instrumentos, é possível evitar erros que podem comprometer a qualidade dos produtos e a segurança dos processos. Neste artigo, abordaremos a importância da calibração de manômetros, os procedimentos envolvidos e os benefícios de manter esses dispositivos sempre em conformidade.
1. Importância da Calibração de Manômetros na Indústria
A calibração de manômetros é um aspecto crucial na operação de diversos setores industriais, pois esses instrumentos são responsáveis por medir a pressão de gases e líquidos em sistemas variados. A precisão dessas medições é vital para garantir a segurança, a eficiência e a qualidade dos processos produtivos. Quando um manômetro não está devidamente calibrado, os resultados podem ser imprecisos, levando a decisões erradas que podem resultar em falhas operacionais, desperdício de recursos e até mesmo riscos à segurança dos trabalhadores.
Um dos principais motivos para a calibração de manômetros é a necessidade de conformidade com normas e regulamentos. Muitas indústrias, como a farmacêutica, alimentícia e petroquímica, são rigorosamente regulamentadas e exigem que todos os equipamentos de medição estejam calibrados e certificados. Isso não apenas assegura a qualidade do produto final, mas também protege a empresa de possíveis sanções legais e prejuízos financeiros. A calibração regular ajuda a manter a conformidade com as normas de segurança e qualidade, evitando problemas que podem surgir devido a medições imprecisas.
Além da conformidade, a calibração de manômetros é essencial para a segurança operacional. Em muitos processos industriais, a pressão inadequada pode levar a situações perigosas, como explosões, vazamentos ou falhas de equipamentos. Por exemplo, em sistemas de vapor, a pressão deve ser monitorada de perto para evitar superaquecimento e danos ao equipamento. A calibração garante que os manômetros estejam fornecendo leituras precisas, permitindo que os operadores tomem decisões informadas e mantenham a segurança do ambiente de trabalho.
Outro ponto importante é a eficiência operacional. Manômetros calibrados corretamente ajudam a otimizar processos, reduzindo o consumo de energia e recursos. Quando as medições de pressão são precisas, os operadores podem ajustar os parâmetros do processo de forma mais eficaz, resultando em uma produção mais eficiente e econômica. Isso é especialmente relevante em indústrias onde a pressão desempenha um papel crítico na qualidade do produto, como na fabricação de produtos químicos e na produção de alimentos e bebidas.
A calibração de manômetros também contribui para a longevidade dos equipamentos. Instrumentos que não são calibrados regularmente podem sofrer desgaste prematuro e falhas, resultando em custos elevados de manutenção e substituição. Ao garantir que os manômetros estejam sempre em conformidade, as empresas podem prolongar a vida útil de seus equipamentos e reduzir os custos operacionais a longo prazo. Isso é particularmente importante em ambientes industriais, onde o investimento em equipamentos é significativo e a manutenção adequada é essencial para a continuidade das operações.
Além disso, a calibração de manômetros é uma prática que promove a cultura de qualidade dentro da organização. Ao estabelecer procedimentos de calibração regulares, as empresas demonstram seu compromisso com a excelência e a melhoria contínua. Isso não apenas aumenta a confiança dos funcionários na precisão dos instrumentos, mas também melhora a moral da equipe, pois todos se sentem parte de um processo que valoriza a qualidade e a segurança.
É importante ressaltar que a calibração deve ser realizada por profissionais qualificados e utilizando equipamentos de referência apropriados. A calibração inadequada pode resultar em medições ainda mais imprecisas, comprometendo todos os esforços feitos para garantir a precisão. Portanto, as empresas devem investir em treinamento e em serviços de calibração de alta qualidade para garantir que seus manômetros estejam sempre em condições ideais de operação.
Por fim, a calibração de manômetros não deve ser vista apenas como uma obrigação regulatória, mas como uma estratégia essencial para a operação bem-sucedida de qualquer instalação industrial. Ao priorizar a calibração, as empresas podem garantir a segurança, a eficiência e a qualidade de seus processos, resultando em produtos finais que atendem ou superam as expectativas dos clientes.
Além da calibração de manômetros, é fundamental considerar a calibração de válvulas de segurança, que também desempenha um papel crucial na manutenção da segurança e eficiência dos sistemas industriais. A interdependência entre esses componentes destaca a importância de uma abordagem holística para a calibração e manutenção de equipamentos em ambientes industriais.
2. Tipos de Manômetros e Seus Usos
Os manômetros são instrumentos essenciais para medir a pressão de gases e líquidos em uma variedade de aplicações industriais. Existem diferentes tipos de manômetros, cada um projetado para atender a necessidades específicas e operar em condições variadas. Neste artigo, exploraremos os principais tipos de manômetros e seus usos, destacando a importância de escolher o instrumento adequado para cada aplicação.
Um dos tipos mais comuns de manômetros é o manômetro de tubo em U. Este dispositivo consiste em um tubo em forma de "U" que contém um líquido, geralmente mercúrio ou água. Quando a pressão é aplicada em um dos lados do tubo, o líquido se desloca, permitindo a leitura da pressão em relação à pressão atmosférica. Os manômetros de tubo em U são frequentemente utilizados em laboratórios e em aplicações onde a precisão é fundamental, como em medições de pressão em sistemas de vácuo.
Outro tipo popular é o manômetro de diafragma. Este instrumento utiliza um diafragma flexível que se deforma quando a pressão é aplicada. A deformação do diafragma é convertida em um movimento mecânico que pode ser lido em uma escala. Os manômetros de diafragma são amplamente utilizados em indústrias químicas e petroquímicas, onde a medição de pressões em ambientes corrosivos é necessária. Eles são conhecidos por sua resistência e capacidade de medir pressões baixas com alta precisão.
Os manômetros de bourdon são outro tipo amplamente utilizado. Eles consistem em um tubo curvado que se desdobra quando a pressão é aplicada. O movimento do tubo é transmitido a um ponteiro que indica a pressão em uma escala. Os manômetros de bourdon são versáteis e podem ser usados em uma variedade de aplicações, desde sistemas de aquecimento e refrigeração até medições em processos industriais. Eles são conhecidos por sua robustez e capacidade de medir pressões altas.
Os manômetros digitais têm se tornado cada vez mais populares devido à sua facilidade de uso e precisão. Esses dispositivos utilizam sensores eletrônicos para medir a pressão e exibem os resultados em um display digital. Os manômetros digitais são ideais para aplicações que exigem medições rápidas e precisas, como em laboratórios e na indústria automotiva. Além disso, muitos modelos digitais oferecem recursos adicionais, como armazenamento de dados e conectividade com computadores, facilitando a análise e o monitoramento das medições.
Os manômetros de pressão diferencial são projetados para medir a diferença de pressão entre dois pontos. Eles são frequentemente utilizados em sistemas de ventilação e climatização, onde é importante monitorar a pressão em diferentes seções do sistema. Esses manômetros ajudam a garantir que o fluxo de ar esteja equilibrado e que os sistemas operem de maneira eficiente. A medição da pressão diferencial é crucial para otimizar o desempenho de sistemas HVAC e garantir a qualidade do ar interior.
Além dos tipos mencionados, existem manômetros específicos para aplicações industriais, como manômetros de pressão absoluta e manômetros de pressão relativa. Os manômetros de pressão absoluta medem a pressão em relação ao vácuo absoluto, enquanto os manômetros de pressão relativa medem a pressão em relação à pressão atmosférica. A escolha entre esses tipos depende das necessidades específicas da aplicação e das condições em que o manômetro será utilizado.
Os manômetros também são utilizados em processos de ensaio e teste, como no ensaio de líquido penetrante, onde a pressão é monitorada para garantir a integridade de materiais e estruturas. Esses testes são essenciais em indústrias como a aeronáutica e a automotiva, onde a segurança e a confiabilidade dos componentes são cruciais.
Em resumo, a escolha do tipo de manômetro adequado é fundamental para garantir medições precisas e confiáveis em diversas aplicações industriais. Cada tipo de manômetro possui características específicas que o tornam mais adequado para determinadas condições e requisitos. Ao entender os diferentes tipos de manômetros e seus usos, as empresas podem otimizar seus processos e garantir a segurança e a eficiência de suas operações.
3. Procedimentos para Calibração de Manômetros
A calibração de manômetros é um processo essencial para garantir a precisão das medições de pressão em diversos setores industriais. A calibração adequada não apenas assegura que os instrumentos estejam funcionando corretamente, mas também ajuda a manter a conformidade com normas e regulamentos. Neste artigo, abordaremos os procedimentos para a calibração de manômetros, destacando as etapas necessárias para garantir resultados confiáveis.
O primeiro passo no processo de calibração é a preparação do ambiente e dos equipamentos. É fundamental escolher um local adequado, onde as condições de temperatura e umidade sejam controladas, pois essas variáveis podem afetar as medições. Além disso, é importante ter à disposição todos os instrumentos necessários, como um manômetro de referência calibrado, uma fonte de pressão e ferramentas para a instalação e ajuste do manômetro a ser calibrado.
Uma vez que o ambiente esteja preparado, o próximo passo é conectar o manômetro a ser calibrado à fonte de pressão. Essa conexão deve ser feita de forma segura, garantindo que não haja vazamentos que possam comprometer as medições. É recomendável utilizar mangueiras e conexões apropriadas para evitar qualquer tipo de contaminação ou interferência nas leituras. Após a conexão, é importante verificar se o manômetro está em boas condições de funcionamento, sem danos visíveis ou sinais de desgaste.
Com o manômetro conectado, o próximo passo é aplicar pressão. Isso pode ser feito utilizando uma bomba de pressão ou um sistema de calibração que permita ajustar a pressão de forma controlada. É importante começar com uma pressão baixa e, em seguida, aumentar gradualmente até atingir a pressão máxima que o manômetro pode medir. Durante esse processo, é fundamental monitorar as leituras do manômetro a ser calibrado e compará-las com as leituras do manômetro de referência.
Ao aplicar a pressão, as leituras devem ser registradas em intervalos específicos. Por exemplo, pode-se registrar as leituras a cada 10% da faixa de medição do manômetro. Isso permitirá uma análise mais detalhada do desempenho do manômetro e ajudará a identificar qualquer desvio em relação ao padrão. Se o manômetro a ser calibrado apresentar leituras que estejam fora da tolerância aceitável em relação ao manômetro de referência, ajustes devem ser feitos.
Os ajustes podem ser realizados utilizando os mecanismos de calibração do manômetro, que geralmente incluem um parafuso de ajuste ou um botão de calibração. É importante seguir as instruções do fabricante para realizar esses ajustes corretamente. Após cada ajuste, a pressão deve ser reaplicada e as leituras devem ser registradas novamente para verificar se o manômetro agora está dentro da faixa de tolerância.
Uma vez que todas as pressões tenham sido aplicadas e as leituras registradas, é hora de analisar os dados coletados. Essa análise deve incluir a comparação das leituras do manômetro a ser calibrado com as do manômetro de referência. Se as leituras estiverem dentro da tolerância especificada, o manômetro pode ser considerado calibrado. Caso contrário, pode ser necessário repetir o processo de ajuste e verificação até que o manômetro esteja funcionando corretamente.
Após a calibração, é importante documentar todo o processo. Essa documentação deve incluir as condições de calibração, as leituras registradas, os ajustes realizados e a data da calibração. Manter registros precisos é fundamental para garantir a rastreabilidade e a conformidade com as normas de qualidade. Além disso, essa documentação pode ser útil para futuras calibrações e inspeções.
Outro aspecto importante a ser considerado é a frequência de calibração. A calibração de manômetros deve ser realizada regularmente, de acordo com as recomendações do fabricante e as normas da indústria. Fatores como o uso intenso do manômetro, mudanças nas condições ambientais e a natureza do processo em que o manômetro está inserido podem influenciar a frequência necessária para a calibração. Em alguns casos, pode ser necessário realizar calibrações mais frequentes, especialmente em ambientes críticos, como na inspeção de caldeiras e em processos industriais onde a precisão é vital.
Por fim, é importante ressaltar que a calibração deve ser realizada por profissionais qualificados e experientes. A calibração inadequada pode resultar em medições imprecisas, comprometendo a segurança e a eficiência dos processos. Portanto, investir em treinamento e em serviços de calibração de alta qualidade é essencial para garantir que os manômetros estejam sempre em condições ideais de operação.
Em resumo, os procedimentos para a calibração de manômetros envolvem a preparação do ambiente, a conexão do manômetro à fonte de pressão, a aplicação controlada de pressão, o registro e análise das leituras, a realização de ajustes e a documentação do processo. Seguir essas etapas com rigor garantirá que os manômetros estejam sempre calibrados e prontos para fornecer medições precisas e confiáveis.
4. Frequência Recomendada para Calibração
A calibração de manômetros é um processo essencial para garantir a precisão e a confiabilidade das medições de pressão em diversos setores industriais. No entanto, a eficácia desse processo depende não apenas da calibração em si, mas também da frequência com que ela é realizada. Neste artigo, discutiremos a frequência recomendada para a calibração de manômetros, considerando fatores que influenciam essa necessidade e as melhores práticas para garantir medições precisas ao longo do tempo.
A frequência de calibração de manômetros pode variar significativamente dependendo de vários fatores, incluindo o tipo de manômetro, a aplicação em que está sendo utilizado, as condições ambientais e a intensidade de uso. Em geral, recomenda-se que a calibração seja realizada pelo menos uma vez por ano. No entanto, em ambientes críticos ou em aplicações onde a precisão é vital, como na indústria farmacêutica ou na produção de alimentos, a calibração pode precisar ser realizada com mais frequência.
Um dos principais fatores que influenciam a frequência de calibração é a natureza do processo em que o manômetro está inserido. Em processos que envolvem altas pressões, temperaturas extremas ou substâncias corrosivas, os manômetros podem sofrer desgastes mais rapidamente. Nesses casos, é aconselhável realizar calibrações trimestrais ou semestrais para garantir que as medições permaneçam precisas. Além disso, em aplicações onde a segurança é uma preocupação, como em sistemas de vapor ou gás, a calibração frequente é crucial para evitar acidentes e garantir a integridade dos equipamentos.
Outro fator a ser considerado é a intensidade de uso do manômetro. Manômetros que são utilizados continuamente em operações críticas podem exigir calibrações mais frequentes do que aqueles que são usados esporadicamente. Por exemplo, em uma planta de produção onde os manômetros estão constantemente monitorando a pressão em sistemas de produção, a calibração pode ser necessária a cada três meses. Por outro lado, manômetros que são usados apenas ocasionalmente podem ser calibrados anualmente, desde que não apresentem sinais de desgaste ou imprecisão.
As condições ambientais também desempenham um papel importante na determinação da frequência de calibração. Fatores como temperatura, umidade e vibração podem afetar o desempenho dos manômetros. Em ambientes onde as condições são extremas ou variáveis, a calibração deve ser realizada com mais frequência. Por exemplo, em locais onde há grandes variações de temperatura, os manômetros podem precisar ser calibrados a cada seis meses para garantir que as medições permaneçam precisas.
Além disso, é importante considerar a política de manutenção da empresa e as recomendações do fabricante do manômetro. Muitos fabricantes fornecem diretrizes específicas sobre a frequência de calibração com base nas características do instrumento e nas condições de operação. Seguir essas recomendações é fundamental para garantir a precisão e a confiabilidade das medições. Além disso, manter um registro detalhado das calibrações realizadas, incluindo datas e resultados, pode ajudar a identificar padrões e determinar a frequência ideal para cada manômetro. Essa prática é conhecida como memória de cálculo e é uma ferramenta valiosa para a gestão de ativos e a manutenção preventiva.
Outro aspecto a ser considerado é a realização de calibrações em resposta a eventos específicos. Se um manômetro sofrer um impacto físico, como uma queda ou um choque, ou se houver uma alteração significativa nas condições de operação, é recomendável realizar uma calibração imediata. Esses eventos podem comprometer a precisão do manômetro e, portanto, a calibração deve ser feita para garantir que as medições estejam corretas.
Por fim, a cultura de qualidade dentro da organização também pode influenciar a frequência de calibração. Empresas que priorizam a qualidade e a segurança tendem a realizar calibrações mais frequentes, independentemente das exigências regulamentares. Essa abordagem proativa ajuda a garantir que os manômetros estejam sempre em conformidade e que as medições sejam precisas, resultando em processos mais eficientes e seguros.
Em resumo, a frequência recomendada para a calibração de manômetros varia de acordo com diversos fatores, incluindo a natureza do processo, a intensidade de uso, as condições ambientais e as diretrizes do fabricante. Embora a calibração anual seja uma prática comum, ambientes críticos e aplicações de alta pressão podem exigir calibrações mais frequentes. Manter registros detalhados e seguir as melhores práticas de calibração ajudará a garantir que os manômetros permaneçam precisos e confiáveis ao longo do tempo, contribuindo para a segurança e a eficiência das operações industriais.
5. Erros Comuns na Calibração de Manômetros
A calibração de manômetros é um processo crítico para garantir a precisão das medições de pressão em diversas aplicações industriais. No entanto, existem vários erros comuns que podem ocorrer durante esse processo, comprometendo a eficácia da calibração e, consequentemente, a confiabilidade dos dados obtidos. Neste artigo, discutiremos os erros mais frequentes na calibração de manômetros e como evitá-los.
Um dos erros mais comuns é a falta de preparação adequada do ambiente de calibração. A calibração deve ser realizada em um local controlado, onde as condições de temperatura e umidade sejam estáveis. Se o ambiente não for adequado, as medições podem ser afetadas, resultando em leituras imprecisas. É fundamental garantir que o local esteja livre de vibrações, correntes de ar e outras interferências que possam influenciar os resultados. Além disso, a limpeza do equipamento e das conexões é essencial para evitar contaminações que possam afetar as medições.
Outro erro frequente é a escolha inadequada do manômetro de referência. O manômetro de referência deve ser um instrumento calibrado e certificado, com precisão superior ao manômetro que está sendo calibrado. Se o manômetro de referência não for confiável, as medições do manômetro a ser calibrado também não serão. Portanto, é crucial verificar a calibração do manômetro de referência antes de iniciar o processo de calibração.
A conexão inadequada entre o manômetro a ser calibrado e a fonte de pressão é outro erro comum. Se houver vazamentos nas conexões, as medições podem ser comprometidas. É importante utilizar mangueiras e conexões apropriadas, garantindo que estejam bem fixadas e livres de vazamentos. Antes de iniciar a calibração, deve-se verificar se todas as conexões estão seguras e se não há sinais de desgaste ou danos.
Durante a aplicação da pressão, um erro comum é a aplicação de pressão de forma abrupta. A pressão deve ser aumentada gradualmente, permitindo que o manômetro a ser calibrado se ajuste às novas condições. A aplicação rápida de pressão pode causar picos que comprometem as medições e danificam o manômetro. Portanto, é importante utilizar uma bomba de pressão ou um sistema de calibração que permita um aumento controlado da pressão.
Outro erro que pode ocorrer é a falta de registro das leituras durante o processo de calibração. É fundamental registrar as leituras em diferentes pontos de pressão para realizar uma análise adequada do desempenho do manômetro. Sem esses registros, pode ser difícil identificar desvios ou problemas que precisam ser corrigidos. Além disso, a documentação das calibrações é essencial para garantir a rastreabilidade e a conformidade com as normas de qualidade.
Um erro adicional é a falta de ajustes adequados após a calibração. Se o manômetro a ser calibrado apresentar leituras fora da tolerância aceitável, é necessário realizar ajustes. Ignorar essa etapa pode resultar em medições imprecisas e comprometer a segurança e a eficiência dos processos. É importante seguir as instruções do fabricante para realizar os ajustes corretamente e, em seguida, reaplicar a pressão para verificar se as leituras estão dentro da faixa de tolerância.
Além disso, a calibração deve ser realizada por profissionais qualificados e experientes. Um erro comum é a falta de treinamento adequado para os operadores que realizam a calibração. A calibração inadequada pode resultar em medições imprecisas e comprometer a segurança dos processos. Portanto, investir em treinamento e capacitação é fundamental para garantir que a calibração seja realizada de forma correta e eficiente.
Outro aspecto a ser considerado é a frequência de calibração. Um erro comum é a calibração irregular ou a falta de um cronograma de calibração. A calibração deve ser realizada de acordo com as recomendações do fabricante e as normas da indústria. Ignorar a necessidade de calibração regular pode resultar em medições imprecisas e comprometer a qualidade dos produtos e a segurança dos processos. Portanto, é importante estabelecer um cronograma de calibração e seguir rigorosamente as diretrizes estabelecidas.
Por fim, a falta de comunicação entre as equipes envolvidas no processo de calibração pode levar a erros. É fundamental que todos os envolvidos estejam cientes dos procedimentos e das expectativas em relação à calibração. A comunicação clara e eficaz ajuda a garantir que todos os passos sejam seguidos corretamente e que os resultados sejam confiáveis.
Em resumo, os erros comuns na calibração de manômetros incluem a falta de preparação do ambiente, a escolha inadequada do manômetro de referência, conexões inadequadas, aplicação abrupta de pressão, falta de registro das leituras, ajustes inadequados, falta de treinamento, calibração irregular e falta de comunicação. Ao estar ciente desses erros e implementar medidas para evitá-los, as empresas podem garantir que seus manômetros estejam sempre calibrados e prontos para fornecer medições precisas e confiáveis.
6. Benefícios da Calibração Regular para a Precisão das Medições
A calibração regular de manômetros é uma prática essencial em diversos setores industriais, pois garante a precisão das medições de pressão. A precisão das medições é fundamental para a segurança, eficiência e qualidade dos processos. Neste artigo, discutiremos os principais benefícios da calibração regular e como ela contribui para a confiabilidade das medições em ambientes industriais.
Um dos principais benefícios da calibração regular é a garantia de medições precisas. Com o tempo, os manômetros podem sofrer desgastes ou desajustes que afetam sua capacidade de fornecer leituras corretas. A calibração regular ajuda a identificar e corrigir esses problemas, assegurando que os manômetros estejam sempre operando dentro das especificações. Isso é especialmente importante em indústrias onde a precisão é crítica, como na farmacêutica, alimentícia e petroquímica, onde até pequenas variações na pressão podem ter consequências significativas.
Além de garantir a precisão, a calibração regular também contribui para a segurança operacional. Em muitos processos industriais, a pressão inadequada pode levar a situações perigosas, como explosões, vazamentos ou falhas de equipamentos. Ao manter os manômetros calibrados, as empresas podem monitorar a pressão de forma eficaz e tomar decisões informadas para evitar acidentes. Isso é particularmente relevante em sistemas de vapor, gás e em processos que envolvem substâncias químicas perigosas, onde a segurança dos trabalhadores e a integridade dos equipamentos são prioridades.
Outro benefício importante da calibração regular é a otimização dos processos. Manômetros precisos permitem que os operadores ajustem os parâmetros do processo de forma mais eficaz, resultando em uma produção mais eficiente e econômica. Quando as medições de pressão são confiáveis, as empresas podem reduzir o desperdício de recursos e melhorar a qualidade dos produtos. Isso é especialmente relevante em ambientes competitivos, onde a eficiência operacional pode ser um diferencial significativo.
A calibração regular também ajuda a prolongar a vida útil dos manômetros. Instrumentos que não são calibrados regularmente podem sofrer desgastes prematuros e falhas, resultando em custos elevados de manutenção e substituição. Ao garantir que os manômetros estejam sempre em conformidade, as empresas podem evitar problemas que podem levar a paradas não planejadas e custos adicionais. Isso é particularmente importante em ambientes industriais, onde o investimento em equipamentos é significativo e a manutenção adequada é essencial para a continuidade das operações.
Além disso, a calibração regular promove a conformidade com normas e regulamentos. Muitas indústrias são rigorosamente regulamentadas e exigem que todos os equipamentos de medição estejam calibrados e certificados. A calibração regular ajuda as empresas a manter a conformidade com essas normas, evitando problemas legais e prejuízos financeiros. A documentação das calibrações realizadas também é fundamental para garantir a rastreabilidade e a conformidade com as normas de qualidade.
Outro aspecto a ser considerado é a melhoria da cultura de qualidade dentro da organização. Ao estabelecer procedimentos de calibração regulares, as empresas demonstram seu compromisso com a excelência e a melhoria contínua. Isso não apenas aumenta a confiança dos funcionários na precisão dos instrumentos, mas também melhora a moral da equipe, pois todos se sentem parte de um processo que valoriza a qualidade e a segurança. A calibração regular pode, portanto, ser vista como uma prática que contribui para a construção de uma cultura organizacional voltada para a qualidade.
Além disso, a calibração regular pode resultar em economias financeiras a longo prazo. Embora possa haver custos associados à calibração, esses custos são frequentemente superados pelas economias geradas pela redução de desperdícios, aumento da eficiência e diminuição de falhas operacionais. Empresas que investem em calibração regular podem evitar custos elevados associados a reparos e substituições de equipamentos, além de garantir a continuidade das operações sem interrupções indesejadas.
Por fim, a calibração regular também é uma prática que facilita a integração de novas tecnologias e processos. À medida que as indústrias evoluem e adotam novas tecnologias, a necessidade de medições precisas se torna ainda mais crítica. A calibração regular garante que os manômetros estejam sempre atualizados e prontos para atender às demandas de processos modernos. Isso é especialmente relevante em setores que estão passando por transformações digitais e automação, onde a precisão das medições é fundamental para o sucesso das operações.
Em resumo, os benefícios da calibração regular para a precisão das medições incluem a garantia de medições precisas, a segurança operacional, a otimização dos processos, a prolongação da vida útil dos manômetros, a conformidade com normas e regulamentos, a melhoria da cultura de qualidade, as economias financeiras a longo prazo e a facilitação da integração de novas tecnologias. Ao priorizar a calibração regular, as empresas podem garantir que seus manômetros estejam sempre prontos para fornecer medições confiáveis, contribuindo para a segurança e a eficiência de suas operações.
Em conclusão, a calibração de manômetros é uma prática essencial que não deve ser negligenciada em qualquer setor que dependa de medições precisas de pressão. Através da calibração regular, é possível garantir a precisão e a confiabilidade dos instrumentos, evitando erros que podem comprometer a qualidade dos produtos e a segurança dos processos. Além disso, a calibração contribui para a otimização das operações, prolonga a vida útil dos equipamentos e assegura a conformidade com normas e regulamentos. Portanto, investir em procedimentos adequados de calibração é fundamental para promover a eficiência, a segurança e a qualidade em ambientes industriais, laboratoriais e de saúde.