Calibração de manômetros: como garantir uma maior precisão nas medições
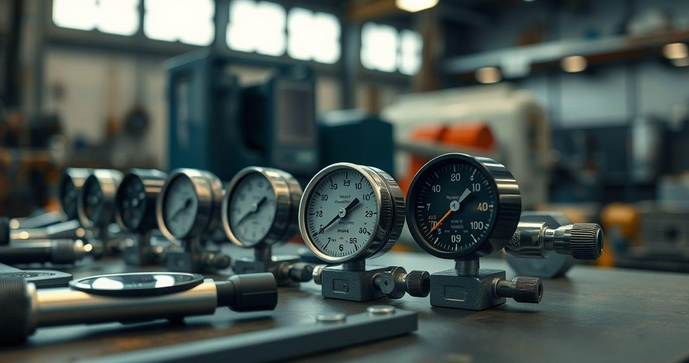
Por: Thiago - 21 de Fevereiro de 2025
A calibração de manômetros é um processo fundamental para garantir a precisão e a confiabilidade das medições em diversos setores, como industrial, laboratorial e de saúde. Com o uso constante desses instrumentos, é essencial realizar a calibração regularmente para evitar erros que podem comprometer a segurança e a eficiência dos processos. Neste artigo, abordaremos a importância da calibração de manômetros, os métodos utilizados, a frequência recomendada e os erros comuns que devem ser evitados.
Importância da Calibração de Manômetros na Indústria
A calibração de manômetros é um aspecto crucial na operação de diversos setores industriais, pois garante que as medições de pressão sejam precisas e confiáveis. Os manômetros são instrumentos utilizados para medir a pressão de gases e líquidos em sistemas variados, desde processos de fabricação até instalações de segurança. A precisão dessas medições é vital para a eficiência operacional, a segurança dos trabalhadores e a conformidade com normas regulatórias.
Um dos principais motivos para a calibração de manômetros é a prevenção de falhas nos equipamentos. Quando um manômetro não está calibrado corretamente, ele pode fornecer leituras imprecisas, levando a decisões erradas na operação de máquinas e processos. Por exemplo, em uma linha de produção, um manômetro que indica uma pressão mais baixa do que a real pode resultar em um aumento no fluxo de um líquido, causando transbordamentos ou danos ao equipamento. Por outro lado, uma leitura de pressão excessiva pode levar a explosões ou falhas catastróficas. Portanto, a calibração regular é essencial para evitar esses riscos e garantir a segurança no ambiente de trabalho.
Além da segurança, a calibração de manômetros também impacta diretamente a eficiência operacional. Processos industriais muitas vezes dependem de medições precisas para otimizar o uso de recursos, como energia e matérias-primas. Um manômetro descalibrado pode resultar em desperdício, aumentando os custos operacionais e reduzindo a competitividade da empresa. Por exemplo, em uma planta de tratamento de água, a pressão inadequada pode afetar a eficiência do sistema de filtragem, resultando em um consumo excessivo de energia e na necessidade de manutenção mais frequente. A calibração regular ajuda a manter os sistemas funcionando de maneira ideal, economizando tempo e recursos.
Outro aspecto importante da calibração de manômetros é a conformidade com normas e regulamentos. Muitas indústrias são obrigadas a seguir padrões específicos de qualidade e segurança, que incluem a calibração de instrumentos de medição. A falta de calibração pode resultar em não conformidade, levando a penalidades financeiras e danos à reputação da empresa. Além disso, a calibração adequada é frequentemente um requisito para a certificação de qualidade, como ISO 9001, que pode ser um diferencial competitivo no mercado. Portanto, manter os manômetros calibrados é uma prática que não apenas garante a segurança e a eficiência, mas também ajuda a cumprir as exigências legais e normativas.
A calibração de manômetros também é fundamental para a manutenção da qualidade do produto. Em indústrias alimentícias e farmacêuticas, por exemplo, a pressão deve ser monitorada com precisão para garantir que os produtos atendam aos padrões de qualidade. Um manômetro descalibrado pode resultar em produtos fora das especificações, levando a desperdícios e à necessidade de retrabalho. Isso não apenas afeta a lucratividade, mas também pode comprometer a confiança do consumidor na marca. Portanto, a calibração regular é uma parte essencial do controle de qualidade em muitos setores.
Além disso, a calibração de manômetros contribui para a longevidade dos equipamentos. Instrumentos que não são calibrados regularmente podem sofrer desgaste prematuro, resultando em falhas e a necessidade de substituição. A calibração ajuda a identificar problemas antes que se tornem críticos, permitindo que as empresas realizem manutenções preventivas e prolonguem a vida útil dos equipamentos. Isso não apenas reduz os custos de manutenção, mas também minimiza o tempo de inatividade, o que é crucial para a continuidade das operações.
Por fim, a calibração de manômetros é uma prática que deve ser incorporada à cultura organizacional das empresas. Treinamentos regulares para os funcionários sobre a importância da calibração e como realizá-la corretamente podem aumentar a conscientização e a responsabilidade em relação à segurança e à eficiência. A implementação de um programa de calibração sistemático, que inclua a documentação das medições e a programação de calibrações regulares, pode ajudar a garantir que todos os manômetros estejam sempre em conformidade e funcionando corretamente.
Em resumo, a calibração de manômetros é de extrema importância na indústria, pois garante a precisão das medições, previne falhas nos equipamentos, melhora a eficiência operacional, assegura a conformidade com normas e regulamentos, mantém a qualidade do produto e prolonga a vida útil dos instrumentos. Para mais informações sobre como realizar a calibração de manômetros, consulte especialistas na área e implemente um programa de calibração eficaz em sua empresa.
Métodos Comuns de Calibração de Manômetros
A calibração de manômetros é um processo essencial para garantir a precisão das medições de pressão em diversos setores industriais. Existem vários métodos utilizados para calibrar esses instrumentos, cada um com suas características e aplicações específicas. Neste artigo, abordaremos os métodos mais comuns de calibração de manômetros, destacando suas vantagens e desvantagens, além de quando cada um deve ser utilizado.
Um dos métodos mais tradicionais de calibração de manômetros é o uso de um manômetro de referência. Este método envolve a comparação do manômetro a ser calibrado com um manômetro de alta precisão, que já foi calibrado e certificado. O manômetro de referência é conectado ao mesmo ponto de medição que o manômetro a ser testado, e as leituras de ambos os instrumentos são comparadas. As diferenças nas leituras permitem que o técnico ajuste o manômetro a ser calibrado, garantindo que ele forneça medições precisas. Este método é amplamente utilizado devido à sua simplicidade e eficácia, mas requer que o manômetro de referência esteja sempre disponível e em boas condições.
Outro método comum é a calibração por pressão estática. Neste método, um dispositivo de calibração, como uma bomba de pressão, é utilizado para gerar uma pressão conhecida no manômetro a ser calibrado. O técnico ajusta a pressão até que o manômetro indique a pressão desejada, e as leituras são registradas em diferentes pontos de pressão. Este método é eficaz para calibrar manômetros em uma ampla faixa de pressão e é frequentemente utilizado em laboratórios de calibração. No entanto, é importante garantir que o equipamento de calibração esteja em boas condições e que as conexões estejam livres de vazamentos para evitar erros nas medições.
A calibração por comparação é outro método utilizado, especialmente em ambientes industriais. Neste caso, um manômetro de referência é utilizado para comparar as leituras do manômetro a ser calibrado em diferentes pontos de pressão. O manômetro de referência deve ser de alta precisão e estar calibrado. As leituras são registradas e comparadas, e qualquer desvio é ajustado. Este método é prático e pode ser realizado no local, mas requer que o manômetro de referência esteja disponível e que o técnico tenha experiência para interpretar os resultados corretamente.
Além desses métodos, a calibração por software tem se tornado cada vez mais comum, especialmente com o avanço da tecnologia. Este método envolve o uso de software especializado que pode se conectar ao manômetro e registrar as leituras automaticamente. O software pode gerar relatórios detalhados e gráficos que ajudam a visualizar o desempenho do manômetro ao longo do tempo. A calibração por software é eficiente e reduz a possibilidade de erro humano, mas requer investimento em tecnologia e treinamento para os operadores.
Outro método que merece destaque é a calibração em campo. Este método é utilizado quando não é prático ou possível levar o manômetro a um laboratório de calibração. Um técnico qualificado realiza a calibração no local, utilizando um manômetro de referência e equipamentos portáteis. A calibração em campo é especialmente útil em indústrias onde o tempo de inatividade deve ser minimizado. No entanto, é importante garantir que as condições ambientais não afetem as medições, como temperatura e umidade.
Além dos métodos mencionados, a memória de cálculo é uma ferramenta importante que pode ser utilizada durante o processo de calibração. A memória de cálculo permite que os técnicos registrem as leituras e os ajustes realizados, facilitando o acompanhamento do desempenho do manômetro ao longo do tempo. Isso é especialmente útil para identificar tendências e prever quando uma nova calibração pode ser necessária. Para mais informações sobre como utilizar a memória de cálculo em processos de calibração, consulte especialistas na área.
Por fim, é importante ressaltar que a escolha do método de calibração deve levar em consideração diversos fatores, como o tipo de manômetro, a faixa de pressão, o ambiente de trabalho e a frequência de uso. Cada método tem suas vantagens e desvantagens, e a seleção adequada pode garantir medições precisas e confiáveis. Além disso, a calibração deve ser realizada regularmente, de acordo com as recomendações do fabricante e as normas da indústria, para garantir a segurança e a eficiência dos processos.
Em resumo, a calibração de manômetros é um processo vital para a operação de diversos setores industriais. Os métodos comuns de calibração, como a comparação com manômetros de referência, calibração por pressão estática, calibração por comparação, calibração por software e calibração em campo, oferecem diferentes abordagens para garantir a precisão das medições. A utilização de ferramentas como a memória de cálculo pode facilitar o acompanhamento e a gestão do desempenho dos manômetros, contribuindo para a eficiência e a segurança das operações industriais.
Frequência Recomendada para Calibração de Manômetros
A calibração de manômetros é uma prática essencial para garantir a precisão e a confiabilidade das medições de pressão em diversos setores industriais. No entanto, a eficácia dessa calibração depende não apenas da qualidade do processo, mas também da frequência com que ela é realizada. Neste artigo, discutiremos a frequência recomendada para a calibração de manômetros, considerando fatores como o tipo de manômetro, o ambiente de operação e as normas regulatórias.
Em geral, a frequência de calibração de manômetros pode variar de acordo com a aplicação e o tipo de manômetro utilizado. Para manômetros que são utilizados em ambientes críticos, como indústrias farmacêuticas e alimentícias, a calibração deve ser realizada com mais frequência. Nesses setores, onde a precisão das medições é vital para a qualidade do produto e a segurança do consumidor, recomenda-se que a calibração ocorra a cada três a seis meses. Isso garante que os instrumentos estejam sempre dentro das especificações e que qualquer desvio seja corrigido rapidamente.
Por outro lado, em aplicações menos críticas, como em processos industriais gerais, a frequência de calibração pode ser estendida. Para manômetros utilizados em ambientes onde as condições de operação são estáveis e onde não há grandes variações de pressão, a calibração pode ser realizada anualmente. No entanto, é importante ressaltar que essa é uma diretriz geral e que cada empresa deve avaliar suas necessidades específicas e os requisitos de seus processos.
Outro fator a ser considerado na determinação da frequência de calibração é o tipo de manômetro. Manômetros mecânicos, por exemplo, podem exigir calibrações mais frequentes do que manômetros digitais, que geralmente são mais estáveis e menos suscetíveis a desvios. Além disso, manômetros que estão sujeitos a condições adversas, como vibrações, temperaturas extremas ou ambientes corrosivos, devem ser calibrados com mais frequência. Essas condições podem afetar a precisão dos instrumentos e, portanto, é fundamental monitorar seu desempenho regularmente.
As normas regulatórias também desempenham um papel importante na definição da frequência de calibração. Muitas indústrias são obrigadas a seguir padrões específicos que estabelecem a frequência mínima de calibração para instrumentos de medição. Por exemplo, a norma ISO 9001, que trata do sistema de gestão da qualidade, recomenda que a calibração de instrumentos de medição seja realizada de acordo com um cronograma estabelecido, que deve ser baseado em fatores como a utilização do instrumento e as condições de operação. Portanto, é fundamental que as empresas estejam cientes das normas aplicáveis ao seu setor e sigam as diretrizes estabelecidas.
Além disso, a implementação de um programa de manutenção preventiva pode ajudar a determinar a frequência ideal de calibração. Ao monitorar o desempenho dos manômetros ao longo do tempo, as empresas podem identificar tendências e prever quando uma nova calibração pode ser necessária. Isso pode ser feito por meio de registros de medições e comparações com os padrões de referência. A utilização de ferramentas como a Treinamento nr 13 pode ser útil para capacitar os funcionários a realizar essas análises e garantir que os manômetros estejam sempre em conformidade.
É importante ressaltar que a calibração não deve ser vista apenas como uma obrigação regulatória, mas como uma prática que contribui para a eficiência e a segurança das operações. A calibração regular ajuda a evitar falhas nos equipamentos, reduzindo o risco de acidentes e garantindo a qualidade dos produtos. Além disso, a calibração adequada pode prolongar a vida útil dos manômetros, resultando em economia de custos a longo prazo.
Por fim, a frequência recomendada para a calibração de manômetros deve ser determinada com base em uma combinação de fatores, incluindo a aplicação, o tipo de manômetro, as condições de operação e as normas regulatórias. As empresas devem estabelecer um cronograma de calibração que atenda às suas necessidades específicas e que garanta a precisão e a confiabilidade das medições. A implementação de um programa de manutenção preventiva e a capacitação dos funcionários são fundamentais para garantir que a calibração seja realizada de forma eficaz e que os manômetros estejam sempre em conformidade.
Em resumo, a frequência de calibração de manômetros é um aspecto crítico para garantir a precisão das medições e a segurança das operações. A calibração deve ser realizada com base nas necessidades específicas de cada setor e nas condições de operação dos instrumentos. Ao seguir as diretrizes recomendadas e implementar um programa de manutenção preventiva, as empresas podem garantir que seus manômetros estejam sempre em conformidade e funcionando corretamente.
Erros Comuns na Calibração de Manômetros e Como Evitá-los
A calibração de manômetros é um processo crítico para garantir a precisão das medições de pressão em diversos setores industriais. No entanto, existem erros comuns que podem ocorrer durante esse processo, comprometendo a eficácia da calibração e, consequentemente, a segurança e a eficiência das operações. Neste artigo, discutiremos os erros mais frequentes na calibração de manômetros e como evitá-los, garantindo que os instrumentos funcionem corretamente.
Um dos erros mais comuns na calibração de manômetros é a falta de um manômetro de referência adequado. Para que a calibração seja eficaz, é essencial utilizar um manômetro de referência que tenha sido calibrado e certificado. Se o manômetro de referência não for preciso, as medições do manômetro a ser calibrado também estarão incorretas. Para evitar esse erro, as empresas devem garantir que o manômetro de referência esteja sempre em boas condições e que tenha um histórico de calibração documentado. Além disso, é importante que os técnicos responsáveis pela calibração sejam treinados para identificar e utilizar manômetros de referência adequados.
Outro erro comum é a não consideração das condições ambientais durante a calibração. Fatores como temperatura, umidade e vibração podem afetar as medições dos manômetros. Por exemplo, se a calibração for realizada em um ambiente com temperaturas extremas, isso pode levar a leituras imprecisas. Para evitar esse problema, é fundamental realizar a calibração em um ambiente controlado, onde as condições possam ser monitoradas e mantidas dentro de limites aceitáveis. Além disso, os técnicos devem estar cientes de como as condições ambientais podem impactar as medições e ajustar os procedimentos de calibração conforme necessário.
A falta de documentação adequada também é um erro que pode comprometer a calibração de manômetros. É essencial registrar todas as medições, ajustes e resultados da calibração para garantir a rastreabilidade e a conformidade com as normas regulatórias. A falta de documentação pode dificultar a identificação de problemas e a implementação de melhorias nos processos de calibração. Para evitar esse erro, as empresas devem estabelecer um sistema de documentação claro e acessível, que permita que todos os envolvidos na calibração possam registrar e consultar informações relevantes.
Outro erro frequente é a realização de calibrações em intervalos inadequados. A calibração deve ser realizada com a frequência recomendada, levando em consideração o tipo de manômetro, as condições de operação e as normas regulatórias. Se a calibração for realizada com pouca frequência, há um risco maior de que os manômetros apresentem desvios significativos. Por outro lado, calibrações excessivas podem resultar em custos desnecessários e interrupções nas operações. Para evitar esse erro, as empresas devem estabelecer um cronograma de calibração baseado em uma análise cuidadosa das necessidades específicas de seus processos e equipamentos.
A falta de treinamento adequado dos técnicos responsáveis pela calibração é outro fator que pode levar a erros. A calibração de manômetros requer conhecimento técnico e habilidades específicas, e a falta de treinamento pode resultar em medições imprecisas e ajustes inadequados. Para evitar esse problema, as empresas devem investir em programas de treinamento, como o curso nr 13, que capacitem os funcionários a realizar calibrações de forma eficaz e segura. O treinamento deve incluir tanto a teoria quanto a prática, garantindo que os técnicos estejam bem preparados para lidar com diferentes tipos de manômetros e situações de calibração.
Além disso, a negligência na manutenção dos equipamentos de calibração pode levar a erros. Os instrumentos utilizados para calibrar manômetros, como bombas de pressão e manômetros de referência, também precisam ser mantidos em boas condições. Se esses equipamentos não forem calibrados ou mantidos adequadamente, suas medições podem ser imprecisas, afetando a calibração dos manômetros. Para evitar esse erro, as empresas devem implementar um programa de manutenção preventiva para todos os equipamentos de calibração, garantindo que estejam sempre prontos para uso.
Por fim, a falta de comunicação entre as equipes envolvidas na calibração pode resultar em erros. É fundamental que todos os membros da equipe estejam cientes dos procedimentos de calibração, das condições de operação e das expectativas em relação aos resultados. A falta de comunicação pode levar a mal-entendidos e erros que comprometem a eficácia da calibração. Para evitar esse problema, as empresas devem promover uma cultura de comunicação aberta e colaboração entre as equipes, garantindo que todos estejam alinhados em relação aos objetivos e procedimentos de calibração.
Em resumo, a calibração de manômetros é um processo crítico que pode ser comprometido por erros comuns, como a falta de um manômetro de referência adequado, a não consideração das condições ambientais, a falta de documentação, a realização de calibrações em intervalos inadequados, a falta de treinamento, a negligência na manutenção dos equipamentos e a falta de comunicação. Ao identificar e evitar esses erros, as empresas podem garantir que seus manômetros estejam sempre calibrados corretamente, contribuindo para a segurança e a eficiência das operações. A implementação de programas de treinamento e manutenção, juntamente com uma comunicação eficaz, são fundamentais para o sucesso da calibração de manômetros.
Em conclusão, a calibração de manômetros é uma prática indispensável para assegurar medições precisas e confiáveis em diversas aplicações industriais e laboratoriais. A realização regular desse processo não apenas previne erros que podem comprometer a segurança e a eficiência, mas também contribui para a qualidade dos produtos e serviços oferecidos. Ao compreender a importância da calibração, os métodos disponíveis, a frequência recomendada e os erros comuns a serem evitados, as empresas podem implementar práticas eficazes que garantam a integridade de seus sistemas de medição. Investir em treinamento adequado e em um programa de manutenção preventiva é essencial para maximizar a eficácia da calibração e, consequentemente, melhorar a operação geral da organização.