Calibração de manômetros é essencial para garantir precisão e segurança em medições industriais
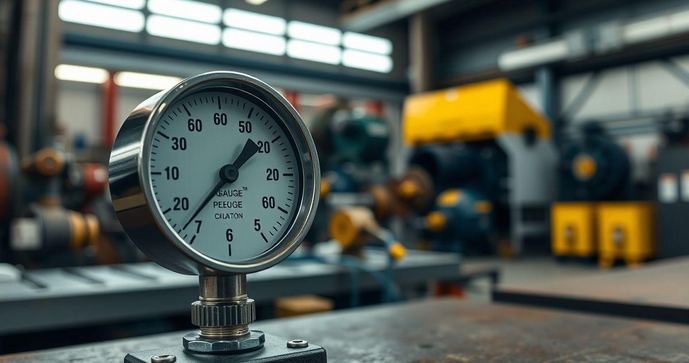
Por: Thiago - 15 de Março de 2025
A calibração de manômetros é um processo fundamental para garantir a precisão e a confiabilidade das medições em diversos setores, como industrial e laboratorial. Através da calibração adequada, é possível evitar erros que podem comprometer a segurança e a eficiência dos processos. Neste artigo, abordaremos a importância da calibração de manômetros, os métodos utilizados, a frequência recomendada e os erros comuns que devem ser evitados.
Importância da Calibração de Manômetros na Indústria
A calibração de manômetros é um aspecto crucial na operação de diversos setores industriais, pois esses instrumentos são responsáveis por medir a pressão de gases e líquidos em sistemas variados. A precisão dessas medições é vital para garantir a segurança, a eficiência e a qualidade dos processos produtivos. Neste contexto, a calibração regular dos manômetros se torna uma prática indispensável.
Um dos principais motivos para a calibração de manômetros é a segurança. Em indústrias que lidam com substâncias perigosas, como produtos químicos ou gases inflamáveis, a medição precisa da pressão é essencial para evitar acidentes. Um manômetro descalibrado pode levar a leituras incorretas, resultando em pressões excessivas ou insuficientes, o que pode causar explosões, vazamentos ou falhas em equipamentos. Portanto, garantir que os manômetros estejam calibrados corretamente é uma medida preventiva que protege não apenas os trabalhadores, mas também o meio ambiente.
Além da segurança, a calibração de manômetros também impacta diretamente a eficiência operacional. Em processos industriais, a pressão correta é fundamental para o funcionamento adequado de máquinas e equipamentos. Por exemplo, em sistemas de aquecimento, a pressão inadequada pode resultar em um desempenho ineficiente, aumentando o consumo de energia e os custos operacionais. Ao realizar a calibração de manômetros regularmente, as indústrias podem otimizar seus processos, reduzindo desperdícios e melhorando a produtividade.
Outro ponto a ser considerado é a qualidade do produto final. Em setores como o alimentício e farmacêutico, a pressão correta é essencial para garantir a qualidade e a segurança dos produtos. Um manômetro descalibrado pode levar a variações na pressão durante a produção, resultando em produtos que não atendem aos padrões de qualidade exigidos. Isso pode resultar em perdas financeiras significativas, além de comprometer a reputação da empresa. Portanto, a calibração regular é uma prática que contribui para a consistência e a qualidade dos produtos fabricados.
Além disso, a calibração de manômetros é uma exigência regulamentar em muitos setores. Organizações de normatização, como a ISO (Organização Internacional de Normalização), estabelecem diretrizes que exigem a calibração de instrumentos de medição para garantir a conformidade com padrões de qualidade e segurança. A não conformidade pode resultar em penalidades, multas e até mesmo a suspensão das operações. Portanto, manter os manômetros calibrados é uma forma de garantir que a empresa esteja em conformidade com as regulamentações aplicáveis.
Outro aspecto importante é a durabilidade dos equipamentos. Manômetros que não são calibrados regularmente podem sofrer desgastes e danos ao longo do tempo, o que pode levar à necessidade de substituições frequentes. A calibração ajuda a identificar problemas precoces, permitindo que as empresas realizem manutenções preventivas e prolonguem a vida útil dos instrumentos. Isso não apenas reduz os custos com a compra de novos manômetros, mas também minimiza o tempo de inatividade dos equipamentos, o que é crucial para a continuidade das operações.
Por fim, a calibração de manômetros também desempenha um papel importante na formação e conscientização dos colaboradores. Ao implementar um programa de calibração regular, as empresas podem educar seus funcionários sobre a importância da precisão nas medições e como isso afeta a segurança e a eficiência. Isso não apenas melhora a cultura de segurança dentro da organização, mas também capacita os colaboradores a identificar e relatar problemas potenciais com os manômetros, contribuindo para um ambiente de trabalho mais seguro e produtivo.
Em resumo, a calibração de manômetros é uma prática essencial na indústria, que impacta diretamente a segurança, a eficiência operacional, a qualidade do produto, a conformidade regulatória e a durabilidade dos equipamentos. Investir em um programa de calibração regular não é apenas uma questão de conformidade, mas uma estratégia inteligente para garantir o sucesso e a sustentabilidade das operações industriais. Portanto, as empresas devem priorizar a calibração de manômetros como parte de suas práticas de manutenção e gestão de qualidade.
Métodos Comuns de Calibração de Manômetros
A calibração de manômetros é um processo essencial para garantir a precisão das medições de pressão em diversos setores industriais. Existem vários métodos utilizados para calibrar esses instrumentos, cada um com suas características e aplicações específicas. Neste artigo, abordaremos os métodos mais comuns de calibração de manômetros, destacando suas vantagens e desvantagens.
Um dos métodos mais tradicionais de calibração é o método de comparação. Neste processo, o manômetro a ser calibrado é comparado a um manômetro de referência, que possui uma precisão conhecida e certificada. O manômetro de referência é conectado ao mesmo ponto de medição que o manômetro em teste, e as leituras de ambos os instrumentos são registradas. A diferença entre as leituras permite determinar se o manômetro em teste está calibrado corretamente ou se precisa de ajustes. Este método é amplamente utilizado devido à sua simplicidade e eficácia, mas requer que o manômetro de referência esteja sempre disponível e em boas condições.
Outro método comum é a calibração por pressão estática. Neste caso, um dispositivo de calibração, como uma bomba de pressão, é utilizado para gerar pressões conhecidas que são aplicadas ao manômetro em teste. O manômetro é então ajustado para que suas leituras correspondam às pressões conhecidas. Este método é particularmente útil para manômetros que operam em faixas de pressão específicas, pois permite uma calibração mais precisa em diferentes pontos da escala. No entanto, a calibração por pressão estática pode ser mais complexa e exigir equipamentos adicionais, como bombas e manômetros de referência.
A calibração por pressão dinâmica é outro método utilizado, especialmente em aplicações onde as pressões variam rapidamente. Neste método, um sistema de teste é projetado para simular as condições reais de operação do manômetro, permitindo que ele seja calibrado em condições dinâmicas. Isso é particularmente importante em indústrias onde as pressões mudam rapidamente, como na petroquímica e na indústria de alimentos e bebidas. A calibração dinâmica pode ser mais desafiadora em termos de configuração e requer equipamentos especializados, mas oferece resultados mais representativos para manômetros que operam em condições variáveis.
Além dos métodos mencionados, a calibração por meio de software também tem ganhado popularidade. Com o avanço da tecnologia, muitos manômetros modernos vêm equipados com interfaces digitais que permitem a calibração por meio de software. Esses sistemas podem ser conectados a computadores ou dispositivos móveis, onde os dados de calibração podem ser registrados e analisados. A utilização de software para calibração oferece vantagens significativas, como a capacidade de armazenar dados históricos, gerar relatórios e realizar análises estatísticas. Além disso, a calibração pode ser realizada de forma mais rápida e eficiente, reduzindo o tempo de inatividade do equipamento.
Um aspecto importante a ser considerado durante a calibração de manômetros é a utilização de uma memória de cálculo. Este recurso permite que os técnicos registrem as leituras e os ajustes realizados durante o processo de calibração, facilitando o acompanhamento e a verificação da precisão ao longo do tempo. A memória de cálculo é especialmente útil em ambientes industriais onde a calibração é realizada com frequência, pois ajuda a manter um histórico detalhado das medições e ajustes, contribuindo para a conformidade com normas e regulamentos.
Outro método que merece destaque é a calibração em campo. Este método é utilizado quando não é viável transportar o manômetro para um laboratório de calibração. Em vez disso, os técnicos realizam a calibração no local de instalação do manômetro, utilizando equipamentos portáteis de calibração. A calibração em campo é prática e eficiente, permitindo que as empresas mantenham a precisão dos manômetros sem interromper suas operações. No entanto, é importante garantir que as condições ambientais sejam controladas, pois fatores como temperatura e umidade podem afetar as medições.
Por fim, a calibração de manômetros deve ser realizada por profissionais qualificados e experientes, que compreendam as especificidades de cada método e as características dos instrumentos. A escolha do método de calibração adequado dependerá de diversos fatores, como o tipo de manômetro, a faixa de pressão, as condições de operação e os requisitos de precisão. Independentemente do método escolhido, a calibração regular é fundamental para garantir a confiabilidade e a segurança das medições de pressão em ambientes industriais.
Em resumo, os métodos comuns de calibração de manômetros incluem a calibração por comparação, pressão estática, pressão dinâmica, calibração por software e calibração em campo. Cada um desses métodos possui suas vantagens e desvantagens, e a escolha do método mais adequado dependerá das necessidades específicas de cada aplicação. A calibração regular é essencial para garantir a precisão e a segurança das medições, contribuindo para a eficiência e a qualidade dos processos industriais.
Frequência Recomendada para Calibração de Manômetros
A calibração de manômetros é uma prática essencial para garantir a precisão e a confiabilidade das medições de pressão em diversos setores industriais. No entanto, a eficácia dessa calibração depende não apenas da qualidade do processo, mas também da frequência com que ela é realizada. Neste artigo, discutiremos a frequência recomendada para a calibração de manômetros, considerando fatores como o tipo de manômetro, as condições de operação e as normas regulatórias.
Em geral, a frequência de calibração de manômetros pode variar de acordo com a aplicação e o ambiente em que estão inseridos. Para manômetros utilizados em processos críticos, como na indústria farmacêutica ou alimentícia, a calibração deve ser realizada com maior frequência, geralmente a cada seis meses. Isso se deve à necessidade de garantir que as medições estejam sempre dentro dos padrões exigidos, uma vez que qualquer variação pode comprometer a qualidade do produto final e a segurança dos consumidores.
Por outro lado, em aplicações menos críticas, como em sistemas de aquecimento ou ventilação, a calibração pode ser realizada anualmente. No entanto, mesmo nesses casos, é importante monitorar o desempenho do manômetro e realizar calibrações adicionais se houver sinais de desvio nas medições. A manutenção preventiva e a calibração regular são fundamentais para evitar problemas futuros e garantir a eficiência dos sistemas.
Outro fator a ser considerado na determinação da frequência de calibração é o tipo de manômetro. Manômetros analógicos, por exemplo, podem exigir calibrações mais frequentes do que os digitais, devido à possibilidade de desgaste mecânico e variações nas leituras. Além disso, manômetros que operam em condições extremas, como altas temperaturas ou pressões, também podem necessitar de calibrações mais frequentes, uma vez que essas condições podem afetar a precisão do instrumento.
As normas regulatórias também desempenham um papel importante na definição da frequência de calibração. Muitas indústrias são obrigadas a seguir diretrizes específicas estabelecidas por órgãos reguladores, como a ISO (Organização Internacional de Normalização) e a ANVISA (Agência Nacional de Vigilância Sanitária). Essas normas geralmente incluem recomendações sobre a frequência de calibração, que devem ser seguidas para garantir a conformidade e a segurança dos processos. Portanto, é fundamental que as empresas estejam cientes das regulamentações aplicáveis ao seu setor e ajustem suas práticas de calibração de acordo.
Além disso, a implementação de um programa de manutenção preventiva pode ajudar a determinar a frequência ideal de calibração. Esse programa deve incluir inspeções regulares dos manômetros, onde os técnicos podem avaliar o desempenho e identificar quaisquer problemas potenciais. Se um manômetro apresentar leituras inconsistentes ou falhas, a calibração deve ser realizada imediatamente, independentemente do cronograma estabelecido. A manutenção proativa é uma estratégia eficaz para evitar falhas e garantir a precisão das medições.
Um aspecto importante a ser considerado é a capacitação dos profissionais responsáveis pela calibração. O Treinamento nr 13 é uma norma que aborda a segurança em caldeiras e vasos de pressão, e inclui diretrizes sobre a calibração de instrumentos de medição. Profissionais bem treinados são mais propensos a realizar calibrações precisas e a identificar problemas que possam afetar a precisão dos manômetros. Portanto, investir em treinamento e capacitação é uma parte essencial da estratégia de calibração de qualquer empresa.
Além da frequência de calibração, é importante também considerar a documentação e o registro das calibrações realizadas. Manter um histórico detalhado das calibrações, incluindo datas, resultados e ajustes feitos, é fundamental para garantir a conformidade com as normas regulatórias e para facilitar auditorias. Essa documentação também pode ser útil para identificar padrões de desempenho e determinar se a frequência de calibração deve ser ajustada ao longo do tempo.
Em resumo, a frequência recomendada para a calibração de manômetros varia de acordo com a aplicação, o tipo de manômetro e as normas regulatórias. Manômetros utilizados em processos críticos devem ser calibrados com mais frequência, enquanto aqueles em aplicações menos críticas podem ter uma frequência anual. A implementação de um programa de manutenção preventiva, a capacitação dos profissionais e a documentação adequada são fatores que contribuem para a eficácia da calibração. Ao seguir essas diretrizes, as empresas podem garantir a precisão e a confiabilidade das medições de pressão, promovendo a segurança e a eficiência em suas operações.
Erros Comuns na Calibração de Manômetros e Como Evitá-los
A calibração de manômetros é um processo crítico para garantir a precisão das medições de pressão em diversos setores industriais. No entanto, erros podem ocorrer durante esse processo, comprometendo a eficácia da calibração e, consequentemente, a segurança e a eficiência das operações. Neste artigo, abordaremos os erros comuns na calibração de manômetros e como evitá-los, garantindo que os instrumentos funcionem corretamente e atendam aos padrões exigidos.
Um dos erros mais frequentes na calibração de manômetros é a falta de um manômetro de referência adequado. A calibração deve ser realizada em comparação com um instrumento de referência que tenha uma precisão conhecida e certificada. Se o manômetro de referência não estiver calibrado ou não for adequado para a faixa de pressão do manômetro em teste, as medições podem ser imprecisas. Para evitar esse erro, é fundamental garantir que o manômetro de referência esteja sempre em boas condições e calibrado de acordo com as normas aplicáveis.
Outro erro comum é a falta de controle das condições ambientais durante a calibração. Fatores como temperatura, umidade e vibração podem afetar as medições de pressão. Por exemplo, a temperatura pode influenciar a densidade do fluido e, consequentemente, a pressão medida. Para evitar esse problema, a calibração deve ser realizada em um ambiente controlado, onde as condições possam ser monitoradas e mantidas dentro dos limites especificados. Além disso, é importante permitir que os instrumentos se aclimatizem à temperatura do ambiente antes de realizar a calibração.
A calibração inadequada do manômetro também é um erro que pode ocorrer. Isso pode acontecer quando o técnico não segue corretamente os procedimentos de calibração ou não ajusta o manômetro de acordo com as especificações do fabricante. Para evitar esse erro, é essencial que os profissionais responsáveis pela calibração sejam devidamente treinados e conheçam os procedimentos corretos. O curso nr 13 é uma excelente oportunidade para capacitar os técnicos em relação às melhores práticas de calibração e segurança em sistemas de pressão.
Outro erro comum é a falta de documentação adequada durante o processo de calibração. Manter registros detalhados das calibrações realizadas, incluindo datas, resultados e ajustes feitos, é fundamental para garantir a conformidade com as normas regulatórias e facilitar auditorias. A ausência de documentação pode levar a problemas de conformidade e dificultar a identificação de padrões de desempenho. Para evitar esse erro, as empresas devem implementar um sistema de registro eficiente que permita o acompanhamento das calibrações e a análise de dados ao longo do tempo.
Além disso, a calibração em intervalos inadequados é um erro que pode comprometer a precisão das medições. A frequência de calibração deve ser determinada com base na aplicação, no tipo de manômetro e nas normas regulatórias. Manômetros utilizados em processos críticos devem ser calibrados com mais frequência, enquanto aqueles em aplicações menos críticas podem ter uma frequência anual. Para evitar esse erro, as empresas devem estabelecer um cronograma de calibração que leve em consideração as necessidades específicas de cada instrumento e as exigências do setor.
Outro aspecto importante a ser considerado é a falta de manutenção preventiva dos manômetros. Instrumentos que não são mantidos adequadamente podem apresentar desgastes e falhas que afetam a precisão das medições. A manutenção preventiva deve incluir inspeções regulares, limpeza e lubrificação dos componentes, além de ajustes conforme necessário. Para evitar esse erro, as empresas devem implementar um programa de manutenção que garanta que os manômetros estejam sempre em boas condições de funcionamento.
Por fim, a falta de comunicação entre as equipes envolvidas na calibração pode levar a erros. É fundamental que todos os profissionais envolvidos no processo de calibração estejam cientes das responsabilidades e dos procedimentos a serem seguidos. A comunicação clara e eficaz entre as equipes de manutenção, operação e calibração é essencial para garantir que todos estejam alinhados e que os processos sejam realizados corretamente. Para evitar esse erro, as empresas devem promover uma cultura de comunicação aberta e colaboração entre as equipes.
Em resumo, os erros comuns na calibração de manômetros incluem a falta de um manômetro de referência adequado, o controle inadequado das condições ambientais, a calibração inadequada, a falta de documentação, a calibração em intervalos inadequados, a falta de manutenção preventiva e a falta de comunicação entre as equipes. Ao identificar e abordar esses erros, as empresas podem garantir a precisão e a confiabilidade das medições de pressão, promovendo a segurança e a eficiência em suas operações. Investir em treinamento e capacitação, como o curso nr 13, é uma estratégia eficaz para minimizar erros e melhorar a qualidade dos processos de calibração.
Em conclusão, a calibração de manômetros é uma prática essencial que não deve ser negligenciada em ambientes industriais e laboratoriais. A precisão nas medições de pressão é crucial para garantir a segurança, a eficiência e a qualidade dos processos. Ao compreender a importância da calibração, os métodos disponíveis, a frequência recomendada e os erros comuns a serem evitados, as empresas podem implementar práticas eficazes que assegurem a confiabilidade de seus instrumentos. Investir em treinamento e capacitação, além de seguir as diretrizes adequadas, é fundamental para manter a integridade dos manômetros e, consequentemente, a segurança e a eficiência das operações. Portanto, a calibração regular deve ser vista como uma prioridade estratégica para qualquer organização que dependa de medições precisas.