Calibração de Manômetros: Importância e Procedimentos
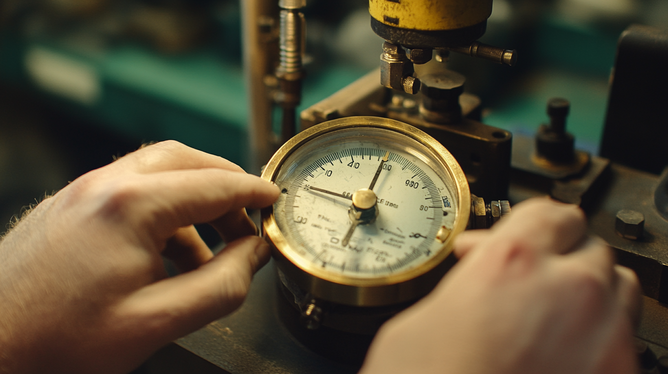
Por: Thiago - 16 de Outubro de 2024
Calibração de manômetros é um aspecto crucial para garantir precisão nas medições de pressão em diversos setores. Neste artigo, vamos abordar a importância da calibração, os procedimentos necessários e os fatores que podem afetar esse processo. Se você deseja garantir a segurança e eficiência de suas operações, continue lendo e descubra tudo sobre a calibração de manômetros.
Importância da Calibração de Manômetros
A calibração de manômetros é um processo essencial em qualquer ambiente onde a medição de pressão é necessária. Manômetros são instrumentos utilizados para medir a pressão de gases ou líquidos em diferentes aplicações, desde indústrias até laboratórios e sistemas de HVAC. A precisão dessas medições é crítica, pois erros nas leituras podem levar a decisões inadequadas, comprometendo a segurança e a eficiência das operações.
Entender a importância da calibração de manômetros implica também conhecer as consequências que podem surgir quando esses instrumentos não estão devidamente calibrados. Erros nas leituras podem resultar em falhas no controle de processos, danos a equipamentos, perda de matéria-prima ou, em casos extremos, até acidentes catastróficos. Portanto, garantir que os manômetros estejam calibrados corretamente não é apenas uma questão de precisão; é uma questão de segurança.
Primeiramente, ao utilizar manômetros não calibrados, você corre o risco de ler pressões que não representam a condição real do sistema. Isso pode levar a uma série de problemas, como o controle inadequado de processos, que pode resultar em sobrecarga ou falhas de equipamentos. Por exemplo, num sistema de boiler, uma leitura errada de pressão pode fazer com que a temperatura alcance níveis perigosos, colocando em risco não apenas o equipamento, mas também a segurança dos operadores.
Ademais, a calibração de manômetros também é vital para a conformidade regulatória. Muitas indústrias necessitam seguir normas específicas que requerem monitoramento rigoroso da pressão. A não conformidade pode resultar em penalizações severas, incluindo multas e fechamento de operações. Portanto, realizar a calibração regularmente é fundamental também para evitar problemas legais e garantir que a empresa esteja em conformidade com as normas da indústria.
Outro aspecto a ser considerado é a economia a longo prazo que a calibração pode proporcionar. Manômetros prontos e bem calibrados ajudam a evitar desperdícios de materiais e recursos. Quando as leituras de pressão estão corretas, os operadores podem otimizar a operação e reduzir o consumo de energia, resultando em economias significativas. Além disso, equipamentos devidamente calibrados tendem a ter uma vida útil mais longa, pois são usados em condições corretas e seguras.
É importante ressaltar que a calibração não é um evento único, mas sim uma prática contínua. A frequência da calibração pode variar dependendo das condições de utilização do manômetro, incluindo ambientes hostis, flutuações de temperatura ou pressão e manipulação frequente. Manômetros usados em ambientes severos precisam ser verificados com mais regularidade, enquanto aqueles em ambientes controlados podem ter intervalos de calibração mais longos.
A calibração deve ser realizada por profissionais qualificados que compreendam a importância dos padrões e equipamentos envolvidos no processo. É fundamental que os técnicos tenham acesso a instrumentos de calibração precisos e certificações adequadas. Além disso, o registro de cada calibração deve ser mantido, garantindo um histórico que possa ser consultado em auditorias futuras.
Manômetros digitais também requerem atenção especial, pois podem apresentar variações de desempenho com o tempo. Alguns modelos exigem a troca de baterias ou manutenção regular dos componentes eletrônicos. Portanto, não basta apenas calibrar, mas também assegurar que o próprio manômetro esteja em boas condições de uso.
Outro aspecto importante a se considerar é a escolha do tipo de manômetro a ser utilizado. Existem diferentes tecnologias disponíveis, como manômetros de tubo de Bourdon, manômetros de piezoelétrico e digitais. Cada um possui suas vantagens e desvantagens e a escolha errada pode impactar na precisão das leituras. Por isso, deve-se realizar uma avaliação cuidadosa das necessidades específicas antes da aquisição.
Finalmente, a calibração de manômetros deve ser encarada como um investimento necessário para a saúde e segurança operacionais. Implementar uma rotina de calibração não só protege os operadores e o ambiente, mas também melhora a eficiência e a confiabilidade dos processos. Para isso, é fundamental criar uma cultura organizacional que priorize a excelência e a atenção detalhada nas medições.
Para concluir, podemos afirmar que a calibração de manômetros é uma prática crucial que garante medições precisas e confiáveis. Desde a segurança operacional até a conformidade regulatória e a economia de recursos, os benefícios de manter manômetros calibrados são evidentes. Portanto, não negligencie essa prática: implemente uma rotina de calibração adequada e invista na qualidade e segurança de suas operações.
Procedimentos para Calibrar Manômetros
Calibrar manômetros é um procedimento técnico vital que assegura a precisão nas leituras de pressão. A calibração envolve o ajuste do instrumento para garantir que as medições se aproximem o máximo possível dos valores reais. Neste artigo, descreveremos os procedimentos adequados para a calibração de manômetros, abordando as etapas necessárias, as ferramentas utilizadas e a importância de seguir adequadamente cada uma delas.
O primeiro passo para calibrar um manômetro é reunir todas as ferramentas e equipamentos necessários. As ferramentas comuns incluem um manômetro padrão ou de referência, um dispositivo de pressão calibrado, um conjunto de adaptadores e conectores, e, em alguns casos, um multímetro para medições elétricas. É essencial que o manômetro padrão possua uma precisão melhor que o manômetro a ser calibrado, pois é ele que servirá de referência durante o processo.
Antes de iniciar a calibração, é importante verificar as especificações do fabricante do manômetro a ser calibrado. Essas informações geralmente estão disponíveis no manual do usuário e fornecem detalhes sobre o intervalo de pressão, método de medição e outros aspectos relevantes. Este conhecimento preliminar ajuda na execução do processo de calibração de forma mais eficaz.
Com todas as ferramentas em mãos e as especificações revisadas, você pode iniciar o processo. O primeiro passo prático é garantir que o manômetro a ser calibrado esteja em boas condições. Inspecione visualmente o instrumento para verificar a presença de danos físicos, corrosão ou vazamentos. Qualquer condição anormal pode afetar a precisão da medição e deve ser corrigida antes de prosseguir.
Após a inspeção inicial, o próximo passo é realizar a conexão do manômetro a ser calibrado ao dispositivo de pressão. Para isso, é necessário utilizar adaptadores e conexões que garantam um encaixe seguro e sem vazamentos. O sistema de pressão deve estar isolado, e o manômetro deve ser conectado ao ponto de teste com cuidado para não causar danos ao equipamento. É importante também garantir que a linha de pressão esteja limpa e livre de contaminantes.
Uma vez conectado, você pode começar a aplicar pressão ao sistema. Inicialmente, pode-se configurar o dispositivo de pressão para uma faixa baixa que se enquadre no escopo do manômetro. Gradualmente, aumente a pressão e registre as leituras em diferentes pontos, como 0, 25%, 50%, 75% e 100% do intervalo de medição do manômetro.
Conforme a pressão for aplicada, faça anotações das leituras exibidas pelo manômetro a ser calibrado e as leituras correspondentes no manômetro de referência. Comparar esses valores é crucial para determinar o erro da leitura. Em um cenário ideal, as leituras devem coincidir, mas pequenos desvios são normais e esperados.
Caso a diferença entre as medições do manômetro de referência e o manômetro sendo calibrado não esteja dentro das tolerâncias especificadas, ajustes deverão ser feitos. Os manômetros mecânicos muitas vezes têm um parafuso de ajuste que pode ser girado para calibrar a precisão. Para manômetros digitais, o processo pode incluir a programação do dispositivo usando um software específico que permite ajustes mais detalhados. Consulte o manual do fabricante para entender os métodos corretos de ajuste.
Após realizar os ajustes necessários, é fundamental repetir o teste de pressão. Aplique os mesmos pontos de pressão e verifique se houve uma melhoria na precisão das medições. Isso deve ser feito até que o manômetro esteja calibrado dentro das tolerâncias aceitáveis. O processo pode ser repetido diversas vezes até que os resultados desejados sejam alcançados.
Uma vez que a calibração foi concluída com sucesso, é importante documentar o procedimento realizado. Cada calibração deve ser registrada em um formato padrão que inclua a data, hora, pessoa responsável, os valores medidos durante os testes, os ajustes feitos e a condição do equipamento. Essas informações são essenciais para auditorias futuras e para manutenção de um histórico confiável da calibração dos equipamentos.
Além disso, é recomendável que a calibração seja realizada em intervalos regulares, mesmo que o instrumento tenha passado nos testes. A frequência da calibração poderá variar de acordo com as condições de uso e as especificações do fabricante. Em ambientes industriais onde as condições são severas, pode ser necessário calibrar os manômetros com mais frequência.
Outra prática benéfica é a realização de testes de verificação periódicos entre as calibrações oficiais. Isso significa realizar medições regulares em pontos críticos de operação, mesmo que não estejam explicitamente agendadas como calibração. Esses testes ajudam a detectar eventuais desvios de medição de forma antecipada, permitindo a correção antes que se tornem críticos.
As calibrações e os testes de verificação devem ser sempre realizados por pessoal treinado e experiente. É importante que os profissionais que realizam as calibrações entendam completamente os princípios de funcionamento dos manômetros e os métodos de calibração. Também devem ser familiarizados com a política de manutenção da empresa e com as normas de segurança pertinentes ao trabalhar em ambientes sob pressão.
Finalmente, envolver todos os membros da equipe que operam os manômetros é crucial. Fornecer treinamento e educação sobre a importância da calibração pode ajudar a criar uma cultura organizacional que prioriza a precisão e a segurança, resultando em um ambiente de trabalho mais eficiente e seguro.
Em resumo, o processo de calibração de manômetros requer a realização de várias etapas para garantir que os instrumentos ofereçam medições precisas. Desde a preparação e conexão ao equipamento, até a documentação do processo, cada passo é crucial para o sucesso da calibração. Um entendimento abrangente das práticas e procedimentos corretos não só melhora a precisão das medições, mas também contribui para a segurança e eficiência das operações.
Fatores que Afetam a Calibração
A calibração de manômetros é uma prática crucial para garantir a precisão nas medições de pressão, mas diversos fatores podem influenciar a eficácia desse processo. Compreender esses fatores é fundamental para garantir que as medições permaneçam dentro dos padrões exigidos de precisão e confiabilidade. Neste artigo, discutiremos os principais fatores que afetam a calibração de manômetros, incluindo condições ambientais, características do próprio instrumento e métodos de uso.
Um dos fatores mais significativos que afetam a calibração de manômetros são as condições ambientais em que o instrumento é utilizado. Mudanças na temperatura, umidade e até mesmo na altitude podem impactar diretamente a precisão das leituras. Por exemplo, a maioria dos manômetros é projetada para funcionar em condições específicas de temperatura. Quando expostos a temperaturas extremas, seu funcionamento pode ser comprometido, resultando em leituras imprecisas.
A umidade também desempenha um papel crítico. Manômetros que contêm componentes eletrônicos são particularmente sensíveis à umidade. A presença de umidade pode causar corrosão e criar circuitos elétricos indesejados, levando a falhas nas medições. Portanto, é importante que os instrumentais sejam adequadamente protegidos de ambientes úmidos, realizando manutenção e calibração em locais onde as condições sejam controladas.
A altitude é outro fator a se considerar. Manômetros que funcionam bem ao nível do mar podem não fornecer leituras precisas em altitudes elevadas devido à diminuição da pressão atmosférica. Isso é especialmente relevante para manômetros utilizados em atividades industriais, como em plataformas de perfuração de petróleo ou em aviões, onde as variações de altitude são significativas. É importante ajustar a calibração com base na altitude em que o manômetro será utilizado.
A manutenção inadequada é outro fator que pode afetar a calibração de manômetros. Se um manômetro não passar por inspeções regulares, pequenos danos ou desgastes podem passar despercebidos, resultando em alterações nas suas características que impactam a precisão. Componentes como vedantes, conexões e tuas calibradas devem ser verificados frequentemente para garantir que o manômetro funcione corretamente. A sujeira acumulada e contaminantes nos tubos ou nas superfícies de medição também podem interferir nas leituras.
A idade do instrumento pode ser um outro fator crítico. Com o passar do tempo, manômetros podem sofrer degradação em seus componentes, mesmo se forem cuidados da maneira adequada. A calibração de um manômetro antigo pode exigir mais atenção e um intervalo de calibração mais frequente, pois as mudanças que ocorrem nos materiais com o tempo podem afetar as medições. A escolha de substituir manômetros mais antigos pode ser uma decisão que deve ser considerada, conforme a confiabilidade das leituras for comprometida.
Além disso, a experiência e o treinamento da equipe que realiza a calibração são fatores determinantes na precisão do processo. Técnicos inexperientes podem cometer erros ao conduzir o processo, seja na conexão dos instrumentos, no ajuste durante a calibração ou na interpretação dos resultados. Portanto, investir em treinamento contínuo e na atualização de conhecimentos dos profissionais é essencial para assegurar a precisão e a qualidade das medições.
Outras variáveis operacionais que podem afetar a calibração incluem pressão de fluídos e vibrações. A pressão de operação dos gases ou líquidos medidos pode impactar a integridade do manômetro. Flutuações bruscas de pressão podem levar ao desgaste dos componentes internos, afetando a precisão das medições ao longo do tempo. É crucial monitorar as condições de operação para garantir que os manômetros não sejam submetidos a pressões além das suas capacidades designadas.
Vibrações excessivas também podem ser prejudiciais para a calibração. Ambientes industriais com alta movimentação e vibrações constantes podem causar desajustes mecânicos em manômetros, levando a leituras ineficazes. Portanto, ao instalar um manômetro, considere a possibilidade de utilizar suportes ou montagens que ajudem a minimizar as vibrações e movimentos indesejados, especialmente em aplicações onde a precisão é crítica.
O tipo de manómetro e sua tecnologia também influenciam a calibração. Manômetros mecânicos e digitais podem ter respostas e características diferentes para a calibração. Por exemplo, manômetros de tubo de Bourdon podem ser mais afetados por fatores físicos externos, enquanto manômetros eletrônicos exigem cuidados especiais com as entradas elétricas e a fonte de alimentação. Cada modelo pode ser suscetível a diferentes fatores de erro, e conhecer esses fatores é primordial para um processo eficaz de calibração.
Outro elemento a considerar são os componentes do sistema em que o manômetro está instalado. A presença de filtros, válvulas ou sistemas de esvaziamento nas linhas pode levar a erros nas medições, especialmente se esses componentes não estiverem funcionando corretamente. Assim, realizar uma análise do sistema completo é essencial e pode impedir erros nos resultados obtidos durante a calibração.
O intervalo de calibração é uma prática que deve ser cuidadosamente considerada e ajustada com base nas condições observadas anteriormente. Se um manômetro estiver operando em condições adversas, pode ser necessário estabelecer um cronograma de calibração mais rigoroso. Cada ambiente e aplicação exigem uma abordagem personalizada para a manutenção das medições, considerando que diferentes condições vão exigir diferentes frequências de calibração.
Finalmente, a qualidade do manômetro também faz uma diferença significativa. Instrumentos de alta qualidade geralmente têm uma melhor estabilidade e precisão nas medições ao longo do tempo. Optar por marcas respeitáveis e instrumentos com boas referências pode reduzir a necessidade de calibrações frequentes e minimizar os fatores de erro ao longo do ciclo de vida do manômetro.
Concluindo, a calibração de manômetros é influenciada por muitos fatores que vão além do simples ato de ajustar o equipamento. Condições ambientais, manutenção regular, experiência da equipe e a qualidade do instrumento são apenas alguns dos aspectos a se considerar. Um compromisso com a atenção às variáveis que afetam a calibração dos manômetros é essencial para garantir medições confiáveis, seguras e precisas. Ao entender e mitigar esses fatores, empresas e profissionais podem melhorar significativamente a qualidade das suas operações e processos industriais.
Manutenção e Verificação de Manômetros Calibrados
A manutenção e verificação de manômetros calibrados são práticas essenciais para garantir a precisão e a confiabilidade de medições de pressão em diversos setores, desde indústrias de manufatura até laboratórios de pesquisa. Um manômetro devidamente mantido não só assegura medições adequadas, mas também contribui para a segurança e eficiência das operações. Neste artigo, discutiremos os melhores métodos para a manutenção e verificação de manômetros, destacando a importância dessas práticas e como realizá-las de maneira eficaz.
A primeira etapa na manutenção de um manômetro é a inspeção visual regular. Isso deve ser feito com uma frequência estabelecida, geralmente a cada mês ou conforme o uso, para identificar quaisquer sinais de desgaste físico, corrosão ou danos. Verifique se há rachaduras ou amassados no corpo do manômetro, e examine as conexões para garantir que não existem vazamentos. Qualquer dano visível pode comprometer a precisão da leitura e deve ser corrigido imediatamente.
Além da inspeção visual, deve-se observar as condições de instalação do manômetro. Posicionar o instrumento em um local adequado é crucial para o seu funcionamento adequado. Manômetros devem ser instalados em áreas onde não estão sujeitos a impactos, vibrações excessivas ou temperaturas extremas. A exposição a condições adversas ao longo do tempo pode resultar em falhas de medição e, em casos extremos, danos irreparáveis ao instrumento.
A manutenção preventiva é uma abordagem eficaz para garantir que os manômetros funcionem de maneira adequada por longos períodos. Esta manutenção pode incluir a limpeza regular dos manômetros, especialmente aqueles em ambientes onde contaminantes, poeira ou umidade estejam presentes. Para manômetros mecanicamente acionados, utilize um pano macio e seco para limpar a superfície e evitar o uso de produtos químicos agressivos que podem danificar o instrumento.
Em sistemas onde manômetros estão sujeitos a pressões elevadas, é importante monitorar frequentemente a pressão de entrada e verificar se este valor está dentro das especificações do fabricante. Exceder a pressão máxima permitida pode comprometer a integridade do manômetro e causar danos permanentes. Ao instalar um manômetro, utilize dispositivos limitadores de pressão sempre que possível para proteger o instrumento contra picos de pressão.
Outro ponto importante a considerar na manutenção é o estado das conexões e vedantes do manômetro. As conexões devem ser mantidas limpas e em bom estado para evitar vazamentos que podem alterar as medições. As vedações devem ser inspecionadas regularmente; se estiverem ressecadas ou deterioradas, é recomendado a troca imediata. A manutenção adequada das conexões e vedantes é crucial para a precisão do manômetro e para a segurança das operações onde ele é utilizado.
A verificação periódica deve ser parte integrante do plano de manutenção dos manômetros. Isso envolve realizar medições em pontos críticos de operação, mesmo que não sejam calibrações formais. Esses testes de verificação ajudam a detectar desvios de medição antes que se tornem problemas maiores. Durante esses testes, compare as leituras do manômetro sob verificação com as medições de um manômetro de referência com maior precisão. Se houver discrepâncias consideráveis, pode ser necessário recalibrar o instrumento.
As verificações devem ser registradas, documentando as leituras de pressão, a data da verificação e qualquer ação corretiva aplicada. Os registros servem não apenas como um histórico da utilização do instrumento, mas também como referência para futuras manutenções e auditorias. Com um histórico detalhado, é possível identificar padrões de falhas ou deterioração, permitindo uma abordagem proativa à manutenção.
Quando se trata de calibração, é fundamental que a mesma seja realizada por profissionais qualificados. A calibração deve ser feita em um ambiente controlado e utilizando equipamentos adequados que garantam a precisão do processo. Se um manômetro foi submetido a condições severas ou se um teste de verificação resultou em medições fora das especificações, uma recalibração deve ser programada imediatamente para evitar o uso de um instrumento com falhas de medição.
Dependendo do tipo de manômetro, pode haver considerações específicas durante o processo de manutenção. Por exemplo, manômetros eletrônicos exigem cuidados com os circuitos e baterias. É importante verificar se as baterias estão com carga adequada e se os conectores elétricos estão limpos e funcionais. Para manômetros mecânicos, a lubrificação pode ser necessária em partes móveis para garantir um funcionamento suave. Em sistemas onde a carga de trabalho é intensa, é necessário monitorar a necessidade de manutenção regularmente.
Outra técnica útil para a manutenção e a verificação de manômetros é a implementação de um programa de manutenção preditiva. Essa abordagem utiliza dados coletados durante a operação para prever falhas antes que ocorram. Sensores e dispositivos que monitoram a pressão, temperatura e vibrações podem fornecer dados cruciais, permitindo que as equipes de manutenção tomem decisões informadas sobre quando realizar calibrações e outras manutenções preventivas.
Além disso, envolvidos em um programa de treinamento dos operadores podem ajudar a reduzir erros humanos que podem afetar as medições. O pessoal deve ser instruído sobre como reconhecer sinais de problemas e sobre a importância de reportar quaisquer anomalias imediatamente. Isso cria uma cultura de segurança e qualidade, onde a precisão das medições é priorizada por todos os membros da equipe.
Por fim, a escolha de manômetros de alta qualidade pode resultar em uma redução considerável nas necessidades de manutenção e verificação. Investir em instrumentos bem projetados e robustos garante que eles possam resistir ao uso constante sem sofrer degradação significativa ao longo do tempo. Além disso, é mais provável que manômetros de marca reconhecida apresentem especificações claras de manutenção, tornando a calibração e verificação mais simples e eficientes.
Em resumo, a manutenção e verificação de manômetros calibrados são fundamentais para garantir a precisão e a segurança nas medições de pressão. Desde inspeções visuais regulares até a implementação de programas de manutenção preditiva, as melhores práticas podem ajudar a maximizar a vida útil dos manômetros. Garantir que o pessoal esteja bem treinado e que a documentação das manutenções seja meticulosa são passos importantes para manter a integridade dos instrumentos. Através de um planejamento cuidadoso e da execução de práticas de manutenção adequadas, você pode assegurar medições precisas e confiáveis ao longo do tempo.
Após explorar a calibração e manutenção de manômetros, fica claro que essas práticas são essenciais para garantir medições precisas e confiáveis. A importância de realizar verificações e calibrações regulares se reflete não apenas na qualidade dos processos industriais, mas também na segurança operacional e na economia de recursos. Fatores como condições ambientais, qualidade do equipamento e experiência da equipe influenciam diretamente os resultados obtidos. Portanto, estabelecer um cronograma robusto de manutenção e verificação, juntamente com um treinamento contínuo para os envolvidos, é fundamental para maximizar a eficiência e a vida útil dos manômetros. Invista em boas práticas de calibração e manutenção e assegure que suas operações funcionem com o mais alto padrão de precisão e segurança.