Calibração de Válvulas de Segurança: Aprenda Aqui!
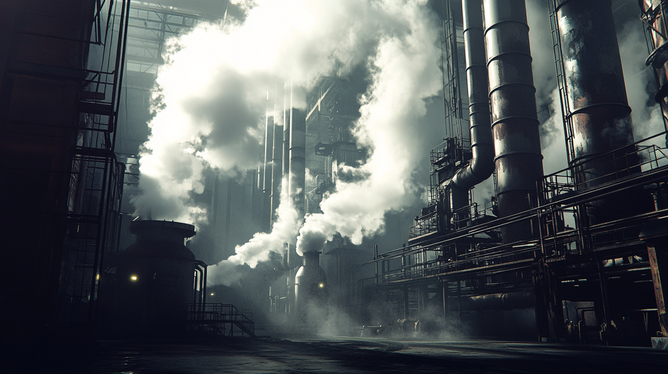
Por: Thiago - 22 de Setembro de 2024
A calibração de válvulas de segurança é fundamental para garantir a segurança e o funcionamento adequado de sistemas industriais. Neste artigo, você descobrirá a importância desse processo, o passo a passo para realizá-lo corretamente e os erros comuns que devem ser evitados. Se você quer garantir a máxima eficiência das válvulas de segurança em sua operação, continue lendo e aprenda tudo o que precisa saber!
Importância da Calibração de Válvulas de Segurança
A calibração de válvulas de segurança é um aspecto crítico em qualquer sistema industrial. Essas válvulas desempenham um papel vital na proteção de equipamentos e processos, evitando acidentes e garantindo a segurança dos operadores e do ambiente. Uma válvula de segurança calibrada corretamente assegura que ela funcione quando necessário e, assim, previne danos catastróficos. Vamos explorar em profundidade a importância da calibração de válvulas de segurança e os benefícios que ela traz para as operações industriais.
Protetores de Sistema
As válvulas de segurança são projetadas para abrir automaticamente quando a pressão no sistema excede um determinado limite, liberando a pressão excessiva e evitando possíveis explosões ou falhas catastróficas. Se uma válvula de segurança não estiver devidamente calibrada, ela pode não abrir na pressão certa, resultando em danos ao equipamento e riscos à segurança. Portanto, a calibração regular é essencial para validar o desempenho da válvula e garantir que ela atue quando necessário.
Padrões de Segurança e Conformidade
Em muitos setores, como petróleo e gás, indústrias químicas e de manufatura, a calibração de válvulas de segurança não é apenas uma boa prática, mas um requisito legal. As regulamentações estabelecem normas específicas que as empresas devem seguir para garantir a segurança. A calibração regular ajuda a garantir que a empresa esteja em conformidade com essas normas, evitando sanções e penalidades. Além disso, isso protege a reputação da empresa e promove um ambiente de trabalho seguro.
Redução de Custos de Manutenção
A calibração pode parecer um custo adicional, mas, na realidade, é um investimento que economiza dinheiro a longo prazo. Válvulas de segurança não calibradas podem resultar em paradas não programadas, reparos dispendiosos e custo de substituições de equipamentos. Além disso, uma válvula de segurança em mau funcionamento pode levar a acidentes que podem resultar em processos judiciais, multas e danos à propriedade. Portanto, implementar um programa de calibração regular não só aumenta a segurança mas também reduz custos operacionais.
Aumento da Vida Útil do Equipamento
A calibração regular das válvulas de segurança pode aumentar a vida útil desses componentes, uma vez que a monitoração e a manutenção ajudam a identificar problemas antes que se tornem sérios. Válvulas bem calibradas funcionam com mais eficiência, são menos propensas a falhas e têm uma vida útil mais longa. Isso significa que as empresas não precisam substituir válvulas com tanta frequência, resultando em economia de custos e um uso mais sustentável dos recursos.
Melhoria na Eficiência Operacional
Válvulas de segurança calibradas corretamente não apenas protegem o sistema, mas também ajudam a otimizar o desempenho geral de uma planta. Válvulas que funcionam de maneira eficiente garantem que as pressões dentro do sistema permaneçam em níveis adequados. Isso significa que a operação pode ser mais eficiente, reduzindo desperdícios e melhorando a produtividade. Além disso, a eficiência operacional não só beneficia a planta, mas também contribui para um menor impacto ambiental.
Gerenciamento de Risco
A calibração de válvulas de segurança é uma parte vital do gerenciamento de riscos em ambientes industriais. Um incidente causado por falhas em válvulas de segurança pode ter consequências catastróficas. Com a calibração, as empresas podem identificar e mitigar riscos antes que eles se tornem uma ameaça real. Isso é especialmente importante em indústrias onde os produtos químicos e as altas pressões estão presentes. Investir em calibração regular faz parte de uma estratégia de gerenciamento de riscos que pode proteger tanto os trabalhadores quanto o equipamento.
Treinamento e Conhecimento da Equipe
A calibração de válvulas de segurança também oferece uma oportunidade para treinar e capacitar a equipe técnica. A realização desse processo exige conhecimento especializado, e quando a equipe é envolvida, isso melhora sua compreensão sobre o funcionamento das válvulas e o sistema como um todo. Isso não só promove um ambiente de trabalho mais seguro, mas também incentiva uma cultura de segurança onde todos estão cientes da importância de manter as válvulas de segurança operacionais e calibradas.
Impacto na Credibilidade e Confiança do Cliente
A segurança industrial afeta diretamente a imagem de uma empresa no mercado. Empresas que demonstram um compromisso com a segurança e a calibração de seus equipamentos são percebidas como mais confiáveis. Isso não só ajuda a atrair novos clientes, mas também a manter relacionamentos com clientes existentes. Investir em calibração de válvulas de segurança é uma maneira de demonstrar um forte compromisso com a segurança, qualidade e eficiência—valores que atraem clientes e parceiros de negócios.
Conclusão
A calibração de válvulas de segurança é um componente essencial em qualquer operação industrial. Não é apenas uma questão de conformidade, mas uma medida proativa que pode salvar vidas, reduzir custos e otimizar operações. O processo deve ser realizado regularmente e cobrir todos os aspectos do desempenho da válvula. Com uma abordagem adequada à calibração, as empresas podem garantir que seus sistemas funcionem da maneira mais segura e eficiente possível.
Processo de Calibração Passo a Passo
A calibração de válvulas de segurança é um processo que requer cuidado e precisão. Essa prática assegura que as válvulas funcionem de acordo com as especificações estabelecidas, garantindo a segurança de equipamentos e operadores. Neste guia, apresentaremos um processo de calibração em etapas detalhadas, proporcionando um entendimento claro e prático de cada fase. Este procedimento é fundamental para manter a eficiência e a eficácia das válvulas de segurança.
Planejamento da Calibração
Antes de iniciar o processo de calibração, um planejamento cuidadoso é imprescindível. Esse planejamento deve incluir:
- Identificação da Válvula: Antes de qualquer coisa, identifique as válvulas de segurança que precisam ser calibradas. Anote as especificações do fabricante e as condições atuais de operação.
- Documentação: Prepare toda a documentação necessária, incluindo diagramas, manuais de operação e registro histórico de manutenção das válvulas.
- Equipamento Adequado: Certifique-se de que você possui todos os instrumentos de calibração e ferramentas necessárias para a execução do serviço, como manômetros, chaves de fenda, e dispositivos de teste de pressão.
- Equipe Treinada: Envolva profissionais treinados e experientes para realizar a calibração, garantindo que todos compreendam o processo e a importância da segurança.
Desconexão e Preparação da Válvula
Após o planejamento, o próximo passo é desconectar a válvula de segurança do sistema:
- Desligar o Sistema: Comece desligando completamente o sistema no qual a válvula está inserida. Isso garantirá a segurança durante o procedimento.
- Liberar a Pressão: Proceda para liberar toda a pressão do sistema para evitar acidentes. Verifique se não há pressão residual na válvula.
- Desconectar Componentes: Remova cuidadosamente a válvula do sistema. Dependendo do tipo de instalação, isso pode exigir a desconexão de flanges ou conexões de solda.
Inspeção Visual da Válvula
Antes de proceder com a calibração, é essencial realizar uma inspeção visual detalhada da válvula:
- Verificação de Danos: Examine a válvula em busca de sinais de desgaste, corrosão ou danos físicos que possam afetar seu funcionamento.
- Condições de Selagem: Confira as condições dos elementos de vedação e garanta que não haja vazamentos ou desgastes.
- Limpeza: Limpe a válvula de qualquer sujeira ou resíduos que possam interferir na calibração.
Calibração da Válvula de Segurança
Com a válvula desconectada e inspecionada, podemos iniciar o processo de calibração propriamente dito:
- Preparação dos Equipamentos de Calibração: Utilize um manômetro de precisão para medir a pressão na qual a válvula deve abrir. Certifique-se de que o instrumento esteja calibrado e dentro do prazo de validade.
- Ajuste da Pressão de Abertura: Lentamente, comece a aumentar a pressão no sistema até que a válvula de segurança deva abrir. O ponto de abertura deve ser o especificado pelo fabricante.
- Teste de Abertura: Observe a válvula para verificar se ela abre no ponto de pressão correto. Se a válvula não abrir conforme o especificado, ajuste-a utilizando os mecanismos de ajuste disponíveis.
- Teste de Fechamento: Após a abertura, reduza a pressão gradualmente para verificar se a válvula se fecha adequadamente e não apresenta vazamentos. Faça anotações dos pontos de ajuste.
Documentação dos Resultados
Após a calibração, é importante documentar todos os resultados observados:
- Registro de Calibração: Anote todas as informações relevantes, incluindo a pressão de abertura e fechamento, anotações sobre a condição da válvula e quaisquer ajustes realizados.
- Histórico de Manutenção: Atualize o histórico de manutenção da válvula, registrando a data da calibração e qualquer outra informação importante que possa ser útil para calibrações futuras.
- Emitir Certificado de Calibração: Se aplicável, emita um certificado de calibração que ateste que a válvula foi calibrada e validada conforme os padrões requeridos.
Reinstalação da Válvula no Sistema
Com a calibração concluída, é tempo de reinstalar a válvula de segurança:
- Reconexão: Reinstale a válvula de segurança no sistema, garantindo que todas as conexões estejam seguras e livres de vazamentos.
- Inspeção Final: Realize uma inspeção final para garantir que tudo está devidamente firme e que não há obstruções ao funcionamento da válvula.
- Reinício do Sistema: Após garantir que a válvula está reinstalada corretamente, reinicie o sistema lentamente, monitorando o funcionamento da válvula durante o processo.
Manutenção Preventiva e Monitoramento Contínuo
A calibração não deve ser um evento isolado. Implementar um programa de manutenção preventiva é fundamental:
- Planos de Calibração Regular: Estabeleça um cronograma de calibração regular para todas as válvulas de segurança, de acordo com as recomendações do fabricante e as normas de segurança.
- Monitoramento Contínuo: Utilize instrumentos de monitoramento para acompanhar constantemente a pressão e o funcionamento das válvulas de segurança.
- Treinamento Contínuo: Promova o treinamento contínuo da equipe técnica para assegurar que todos estejam atualizados sobre as melhores práticas de calibração e manutenção.
Conclusão
A calibração de válvulas de segurança é um processo meticuloso que é vital para garantir a segurança e a eficiência nas operações industriais. Seguir um procedimento passo a passo não só assegura que a válvula funcionará como projetada, mas também protege a integridade dos sistemas em que está instalada. Ao manter um programa regular de calibração e manutenção, as empresas podem aumentar a vida útil de seus equipamentos, reduzir custos e, mais importante, garantir um ambiente de trabalho seguro.
Erros Comuns na Calibração de Válvulas de Segurança
A calibração de válvulas de segurança é um aspecto crítico na manutenção da segurança industrial. No entanto, muitos profissionais costumam cometer erros que podem comprometer a eficácia das válvulas e até colocar em risco a segurança dos trabalhadores e da operação. Neste artigo, abordaremos os erros mais comuns na calibração de válvulas de segurança, além de apresentar recomendações para evitar esses erros e garantir uma calibração eficaz.
Não Realizar a Calibração Regularmente
Um dos erros mais frequentes é não realizar calibrações regulares. Muitos profissionais subestimam a importância da calibração periódica e acreditam que uma única calibração será suficiente para a vida útil da válvula. Contudo, as condições operacionais podem mudar e, com o tempo, a válvula pode perder a precisão.
- Consequências: A falta de calibração regular pode levar a falhas na válvula durante situações críticas. Além disso, pode resultar em danos ao equipamento e riscos de segurança para os trabalhadores.
- Recomendação: Estabeleça um cronograma de calibração de acordo com as recomendações do fabricante e as normas de segurança aplicáveis.
Uso de Equipamentos de Calibração Inadequados
Outro erro comum é a utilização de equipamentos de calibração inadequados ou não calibrados. Manômetros, por exemplo, devem ser calibrados periodicamente para garantir que forneçam medições precisas.
- Consequências: Utilizar ferramentas ou instrumentos de medição com problemas pode levar a resultados imprecisos durante a calibração, tornando as válvulas inseguras e ineficazes.
- Recomendação: Sempre verifique a calibragem dos instrumentos antes do uso e, se necessário, utilize equipamentos de marcas confiáveis e disponíveis no mercado.
Não Realizar Inspeção Visual Prévia
Um erro que pode passar despercebido é a ausência de uma inspeção visual detalhada antes da calibração. Muitas vezes, os técnicos pulam essa etapa, indo direto para a calibração.
- Consequências: Se a válvula apresentar danos ou desgaste e não for identificado antes da calibração, a medição pode não refletir a verdadeira condição da válvula, afetando sua segurança.
- Recomendação: Realize uma inspeção visual detalhada antes de iniciar a calibração. Verifique a integridade e as condições de vedação da válvula.
Ajustes Improvisados em Vez de Calibração Completa
Algumas equipes tentam corrigir problemas de calibração fazendo ajustes improvisados ao invés de realizar uma calibração completa. Essa prática é arriscada e geralmente ineficaz.
- Consequências: Ajustes não documentados podem levar a inconsistências e falhas mais adiante, criando riscos à segurança. Além disso, pode ser difícil rastrear as modificações realizadas.
- Recomendação: Sempre siga o procedimento completo de calibração. Se a válvula estiver fora de especificação, faça os ajustes necessários de acordo com o manual do fabricante.
Ignorar a Documentação de Calibração
A documentação correta é um aspecto crítico da calibração, mas muitos profissionais negligenciam essa etapa, resultando em registros inadequados.
- Consequências: A falta de registros pode dificultar o histórico de manutenção da válvula e a conformidade com as normas de segurança. Isso também pode causar problemas durante auditorias e inspeções.
- Recomendação: Mantenha registros detalhados de cada calibração, incluindo a pressão de abertura, fechamento e quaisquer ajustes realizados.
Desconsiderar as Especificações do Fabricante
Um erro comum é ignorar as especificações e as recomendações do fabricante durante o processo de calibração. Isso pode levar a práticas inadequadas que não são seguras.
- Consequências: Seguir padrões não recomendados pelo fabricante pode resultar em calibrações imprecisas, tornando a válvula insegura e não confiável operações.
- Recomendação: Sempre consulte o manual do fabricante para entender as especificações e recomendações para calibração.
Falta de Treinamento da Equipe
A calibração de válvulas de segurança exige conhecimentos específicos, e a falta de treinamento adequado da equipe é um erro comum e grave.
- Consequências: Técnicos sem treinamento podem cometer erros durante a calibração, resultando em válvulas mal calibradas e falhas operacionais.
- Recomendação: Forneça treinamentos regulares e atualizações para a equipe técnica, garantindo que todos estejam atualizados sobre as melhores práticas de calibração e segurança.
Calibração em Condições Inadequadas
Realizar a calibração em condições inadequadas, como ambientes com vibrações, temperaturas extremas ou sujeira excessiva, é outro erro comum. Esses fatores podem interferir nos resultados de calibração.
- Consequências: A calibração realizada em ambientes não controlados pode resultar em medições incorretas, comprometendo a eficácia da válvula.
- Recomendação: Sempre realize a calibração em condições controladas e adequadas, de preferência em um local limpo, seco e livre de vibrações excessivas.
Descartar o Teste de Funcionamento Pós-Calibração
Após a calibração, muitos técnicos se esquecem de realizar um teste de funcionamento para verificar a eficácia da válvula calibrada. Ignorar essa etapa é um erro sério.
- Consequências: Sem um teste pós-calibração, há um risco elevado de operar uma válvula que não esteja funcionando corretamente, colocando a segurança em risco.
- Recomendação: Sempre realize um teste de funcionamento logo após a calibração para garantir que a válvula está atuando em conformidade com as especificações esperadas.
Resistir à Atualização de Procedimentos
Outra questão é a resistência em atualizar os procedimentos de calibração, mesmo quando as melhores práticas estão mudando. Muitas empresas continuam a seguir antigos protocolos que não são mais eficazes.
- Consequências: Ignorar inovações e melhorias nos procedimentos pode resultar em calibrações inadequadas e falhas nos sistemas de segurança.
- Recomendação: Revise e atualize os procedimentos regularmente, levando em consideração novas tecnologias e práticas recomendadas.
Conclusão
Evitar erros comuns na calibração de válvulas de segurança é essencial para manter a integridade das operações industriais. A implementação de um programa de calibração adequado e a formação contínua da equipe são fundamentais para mitigar riscos e garantir a segurança. Lembre-se de que cada erro pode ter consequências sérias, incluindo riscos à vida e danos ao equipamento. Portanto, siga as diretrizes de calibração e mantenha sua operação segura e eficiente.
A calibração de válvulas de segurança é um componente vital para a segurança e a eficácia dos sistemas industriais. Ao longo deste artigo, abordamos a importância desse processo, detalhamos um passo a passo para garantir uma calibração precisa e discutimos os erros comuns que devem ser evitados. Investir na calibração regular e seguir as melhores práticas não apenas protege o equipamento e os trabalhadores, mas também contribui para a eficiência operacional e a conformidade com regulamentações de segurança. Ao aplicar o conhecimento adquirido aqui, você estará preparando sua operação para um desempenho seguro e confiável. Não subestime a relevância desse processo—garantir a calibração adequada é fundamental para o sucesso a longo prazo de qualquer instalação industrial.